Method for manufacturing bamboo fibers
A manufacturing method and bamboo fiber technology, applied in the field of bamboo fiber manufacturing, can solve the problems of chemical pollution, large pollution, shortening of fiber manufacturing process, etc., and achieve the effect of accelerating the reaction process, reducing chemical pollution, and accelerating the reaction progress
- Summary
- Abstract
- Description
- Claims
- Application Information
AI Technical Summary
Problems solved by technology
Method used
Image
Examples
Embodiment 1
[0037] Take about 1 kg of raw bamboo slices, about 20 cm in length and 1 cm in width. Put it in a roller compactor and crush it several times to form a mesh. Then, it was placed in a 50-liter pressure reactor, and 200 milliliters of 5% NaOH was added to the kettle and stirred evenly. Raise the temperature to heat the reaction kettle and remove the air in the kettle, close the exhaust valve to gradually increase the temperature to 140°C, and at the same time, the pressure gauge shows that the pressure is rising. After heat preservation and pressure holding for 15 minutes, the exhaust valve is quickly and safely opened within 2 seconds, and the pressure is reduced to zero through remote control. The broken fibers and liquid were collected, and the fibers and liquid were separated by a centrifuge for 3 minutes. Boil the separated fibers in boiling water (just submerged) for 3 minutes, centrifuge to separate the fibers and liquid, repeat three times, collect the liquid for extra...
Embodiment 2
[0039] Take about 1 kg of raw bamboo slices, about 20 cm in length and 1 cm in width. Put it in a roller compactor and crush it several times to form a mesh. Then it was placed in a 50-liter pressure reactor, and 200 milliliters of 2% NaCO was added to the kettle, 0.2% sodium sulfite, a mixture of 0.2% sodium dodecylbenzenesulfonate, and stirred evenly. Raise the temperature to heat the reaction kettle and remove the air in the kettle, close the exhaust valve to gradually increase the temperature to 135°C, and the pressure gauge shows that the pressure is rising at the same time. After heat preservation and pressure holding for 20 minutes, quickly and safely open the exhaust valve within 2 seconds to reduce the pressure to zero. The broken fibers and liquid were collected, and the fibers and liquid were separated by a centrifuge for 3 minutes. Boil the separated fibers in boiling water (just submerged) for 5 minutes, centrifuge to separate the fibers and liquid, repeat three...
PUM
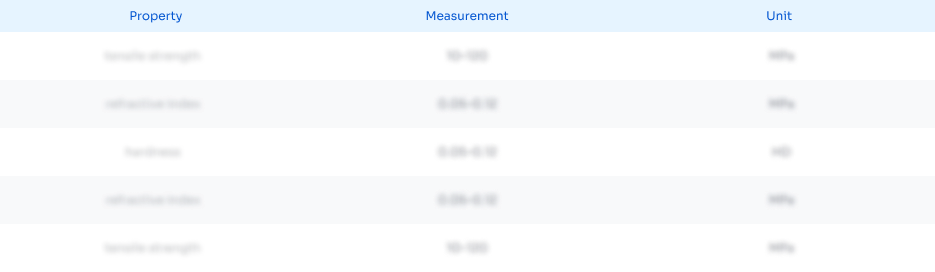
Abstract
Description
Claims
Application Information

- R&D
- Intellectual Property
- Life Sciences
- Materials
- Tech Scout
- Unparalleled Data Quality
- Higher Quality Content
- 60% Fewer Hallucinations
Browse by: Latest US Patents, China's latest patents, Technical Efficacy Thesaurus, Application Domain, Technology Topic, Popular Technical Reports.
© 2025 PatSnap. All rights reserved.Legal|Privacy policy|Modern Slavery Act Transparency Statement|Sitemap|About US| Contact US: help@patsnap.com