Method for preparing cathode roller
A cathode roller, conventional technology, applied in the field of electrochemical applications, can solve the problems affecting the quality of copper foil products, uneven thickness of copper cylinder, uneven cross-sectional area, etc., achieve tight combination, solve uneven thickness, and uniform thickness Effect
- Summary
- Abstract
- Description
- Claims
- Application Information
AI Technical Summary
Problems solved by technology
Method used
Image
Examples
Embodiment 1
[0021] This embodiment is a preparation method for preparing a 1500mm φ1500mm cathode roller. The specific process includes:
[0022] Step 1. Make the cathode roller core; weld the steel cylinder, the auxiliary plate and the rotating shaft to form the cathode roller core;
[0023] Step 2: Relieve stress on the completed cathode roller core; use conventional artificial aging methods to perform stress relief; the temperature of the stress relief is 180° C. and the temperature is kept for 10 hours.
[0024] Step 3: Process the cathode roller core according to conventional machining. During processing, the coaxiality of the steel cylinder and the rotating shaft is guaranteed to be 0.05mm, while the roundness of the steel cylinder is 0.025mm, straightness of 0.036mm, dimensional accuracy φ1476±0.025mm, and surface roughness Ra1.6.
[0025] Step 4, surface deposition; immerse the processed cathode roller core in the electrodeposition solution; connect the cathode roller core to the cathode ...
Embodiment 2
[0031] This embodiment is a preparation method for preparing a φ2000mm cathode roller. The specific process includes:
[0032] Step 1. Make the cathode roller core; weld the steel cylinder, the auxiliary plate and the rotating shaft to form the cathode roller core;
[0033] Step 2: Relieve stress on the completed cathode roller core; use conventional artificial aging methods to perform stress relief; the temperature of the stress relief is 180° C. and the temperature is kept for 10 hours.
[0034] Step 3: Process the cathode roller core according to conventional machining. During processing, the coaxiality of the steel cylinder and the rotating shaft is guaranteed to be 0.05mm, while the roundness of the steel cylinder is 0.03mm, the straightness is 0.05mm, the dimensional accuracy is φ1976±0.03mm, and the surface roughness is Ra1.6.
[0035] Step 4, surface deposition; immerse the processed cathode roller core in the electrodeposition solution; connect the cathode roller core to the ...
Embodiment 3
[0041] This embodiment is a preparation method for preparing a φ2700mm cathode roller. The specific process includes:
[0042] Step 1. Make the cathode roller core; weld the steel cylinder, the auxiliary plate and the rotating shaft to form the cathode roller core;
[0043] Step 2: Relieve stress on the completed cathode roller core; use conventional artificial aging methods to perform stress relief; the temperature of the stress relief is 180° C. and the temperature is kept for 10 hours.
[0044] Step 3: Process the cathode roller core according to conventional machining. During processing, it is necessary to ensure the coaxiality of the steel cylinder and the rotating shaft is 0.06mm, while ensuring the roundness of the steel cylinder is 0.08mm, straightness of 0.08mm, dimensional accuracy φ2676±0.06mm, and surface roughness Ra1.6.
[0045] Step 4, surface deposition; immerse the processed cathode roller core in the electrodeposition solution; connect the cathode roller core to the ...
PUM
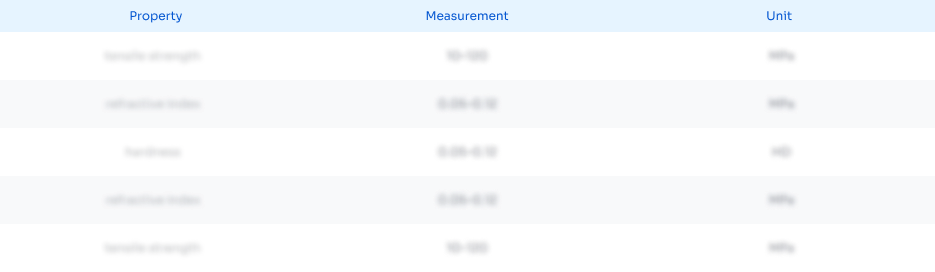
Abstract
Description
Claims
Application Information

- R&D Engineer
- R&D Manager
- IP Professional
- Industry Leading Data Capabilities
- Powerful AI technology
- Patent DNA Extraction
Browse by: Latest US Patents, China's latest patents, Technical Efficacy Thesaurus, Application Domain, Technology Topic, Popular Technical Reports.
© 2024 PatSnap. All rights reserved.Legal|Privacy policy|Modern Slavery Act Transparency Statement|Sitemap|About US| Contact US: help@patsnap.com