Ordinary fine procelain
A technology of fine porcelain and waste porcelain powder, applied in the field of ceramic production, can solve the problems of high energy consumption, high cost, and surrounding environmental pollution, and achieve the effects of saving combustion costs, reducing adverse effects, and saving energy
- Summary
- Abstract
- Description
- Claims
- Application Information
AI Technical Summary
Problems solved by technology
Method used
Examples
Embodiment 1
[0012] The weight percentage components of ordinary fine porcelain blanks are: Guangxi soil 9%; Jingxing soil 5%; Shanyin soil 6%; Yusi soil 2%; Tangxian soil 8%; Longyan soil 10%; Quartz 22%; Datong soil 24%; feldspar 8%; bone china waste porcelain powder 6%.
[0013] After batching according to the above-mentioned ingredients and content, add water ball mill, sieve, filter the mud, knead the mud, shape, kiln fire, and inspect. The blank is crushed and processed into 100-mesh fine powder, and then put into a wet ball mill and added with water for ball milling, material: ball: water = 1:2.5:1, ground for 18-20 hours, passed through a 250-mesh sieve, and the fineness is 0.8%; After being dehydrated by the mud filter to a water content of 21%, under the condition of a vacuum degree ≥ 0.09MPa, the mud is practiced twice in a vacuum mud refining machine, and it is formed by rolling, cold pressing or grouting, and the firing temperature is 1250°C.
Embodiment 2
[0015] The weight percentage components of the fine porcelain blank are: Guangxi soil 12%; Jingxing soil 8%; Shanyin soil 2%; Yusi soil 2%; Tangxian soil 2%; Longyan soil 14%; quartz 22%; Datong soil 24%; feldspar 8%; bone china waste porcelain powder 6%.
[0016] After batching according to the above-mentioned ingredients and content, add water ball mill, sieve, filter the mud, knead the mud, shape, kiln fire, and inspect. The blank is crushed and processed into 100-mesh fine powder, and then put into a wet ball mill and added with water for ball milling, material: ball: water = 1:2.5:1, ground for 18-20 hours, passed through a 250-mesh sieve, and the fineness is 0.8%; After being dehydrated by the mud filter to a water content of 21%, the mud is smelted twice in a vacuum mud refining machine under the condition of a vacuum degree ≥ 0.09MPa, and the mud is formed by cold pressing at a firing temperature of 1250°C.
Embodiment 3
[0018] The weight percentage components of ordinary fine porcelain blanks are: Guangxi soil 9%; Jingxing soil 5%; Shanyin soil 2%; Yusi soil 2%; Tangxian soil 2%; Longyan soil 8%; quartz 22%; Datong soil 30%; feldspar 14%; bone china waste porcelain powder 6%.
[0019] After batching according to the above-mentioned ingredients and content, add water ball mill, sieve, filter the mud, knead the mud, shape, kiln fire, and inspect. The blank is crushed and processed into 100-mesh fine powder, and then put into a wet ball mill and added with water for ball milling, material: ball: water = 1:2.5:1, ground for 18-20 hours, passed through a 250-mesh sieve, and the fineness is 0.8%; After being dehydrated by the mud filter to a water content of 21%, the mud is smelted twice in a vacuum mud refining machine under the condition of a vacuum degree ≥ 0.09MPa, and is formed by rolling at a firing temperature of 1240°C.
PUM
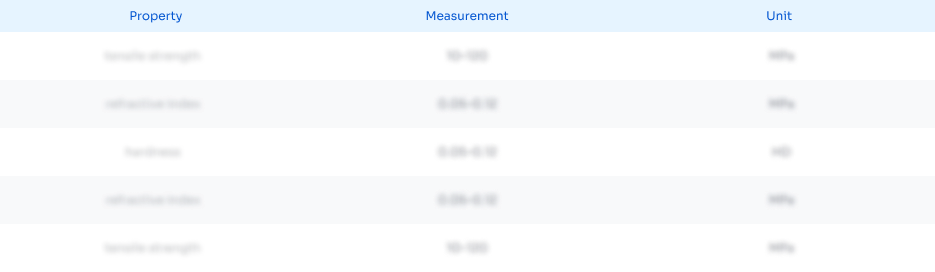
Abstract
Description
Claims
Application Information

- Generate Ideas
- Intellectual Property
- Life Sciences
- Materials
- Tech Scout
- Unparalleled Data Quality
- Higher Quality Content
- 60% Fewer Hallucinations
Browse by: Latest US Patents, China's latest patents, Technical Efficacy Thesaurus, Application Domain, Technology Topic, Popular Technical Reports.
© 2025 PatSnap. All rights reserved.Legal|Privacy policy|Modern Slavery Act Transparency Statement|Sitemap|About US| Contact US: help@patsnap.com