Micro-tension control system of copper-pipe high-speed continuous induction annealing furnace
A micro-tension control and annealing furnace technology, applied in the direction of furnace, furnace type, heat treatment furnace, etc., can solve the problems of copper tube shrinkage or stretching
- Summary
- Abstract
- Description
- Claims
- Application Information
AI Technical Summary
Problems solved by technology
Method used
Image
Examples
Embodiment Construction
[0020] Below in conjunction with accompanying drawing and specific embodiment, further illustrate the present invention, should be understood that these embodiments are only for illustrating the present invention and are not intended to limit the scope of the present invention, after having read the present invention, those skilled in the art will understand various aspects of the present invention Modifications in equivalent forms all fall within the scope defined by the appended claims of this application.
[0021] Refer to attached figure 1 with 2 Described a kind of copper tube high-speed continuous induction annealing furnace micro-tension control system, pinch mechanism 2, speed measuring device 3, annealing furnace 4, traction tensioning device 5, frequency conversion motor 6, frequency conversion speed regulation digital control system 7, and can Programmable logic controller; the traction tension mechanism 5 is provided with an adjustable precision clamping device 8 ...
PUM
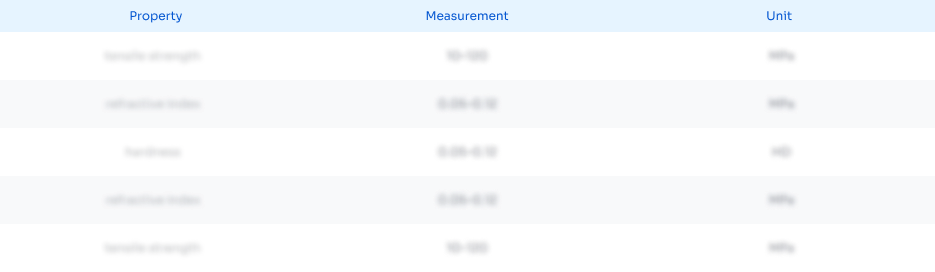
Abstract
Description
Claims
Application Information

- R&D Engineer
- R&D Manager
- IP Professional
- Industry Leading Data Capabilities
- Powerful AI technology
- Patent DNA Extraction
Browse by: Latest US Patents, China's latest patents, Technical Efficacy Thesaurus, Application Domain, Technology Topic, Popular Technical Reports.
© 2024 PatSnap. All rights reserved.Legal|Privacy policy|Modern Slavery Act Transparency Statement|Sitemap|About US| Contact US: help@patsnap.com