Tensioning method for horizontal continuous annealing furnace of cold-rolled sheet processing line
A continuous annealing furnace and cold-rolled sheet technology, applied in heat treatment furnaces, heat treatment equipment, heat treatment process control, etc., can solve problems such as broken strips in zinc pots, improve production efficiency, reduce the risk of broken strips, and control precise tension Effect
- Summary
- Abstract
- Description
- Claims
- Application Information
AI Technical Summary
Problems solved by technology
Method used
Image
Examples
Embodiment 1
[0036] combine figure 1 , a kind of method for building a horizontal continuous annealing furnace of a cold-rolled sheet processing line of the present embodiment. After the furnace area is overhauled, the production stage is resumed, and the strip steel enters the furnace heating area 8 through the transmission of the front tension roll 1 (that is, the 2# tension roll) , the heated strip passes through the heat-stretching roller 4, enters the zinc pot 3, and then runs to the water quenching tank 7 through the pinch roller, and finally is transported to the next process by the rear tension roller 6 (that is, 3# tension roller) . During the entire conveying process of the strip steel, the TM2 tensiometer 2 monitors the actual tension value of the strip steel at the furnace entrance in real time and gives feedback, and the TM3 tensiometer 5 monitors the actual tension value of the strip steel in the water quenching section in real time and gives feedback. Compare with the set t...
PUM
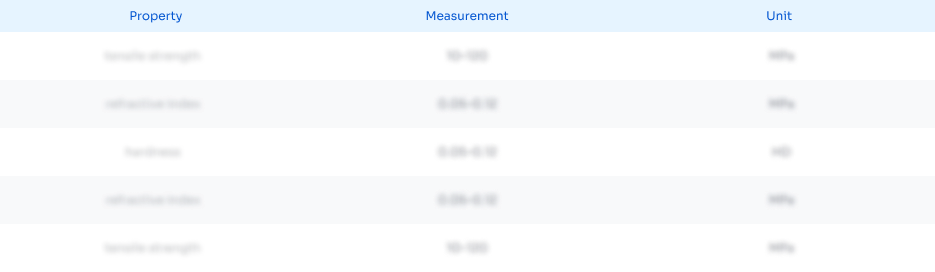
Abstract
Description
Claims
Application Information

- R&D Engineer
- R&D Manager
- IP Professional
- Industry Leading Data Capabilities
- Powerful AI technology
- Patent DNA Extraction
Browse by: Latest US Patents, China's latest patents, Technical Efficacy Thesaurus, Application Domain, Technology Topic, Popular Technical Reports.
© 2024 PatSnap. All rights reserved.Legal|Privacy policy|Modern Slavery Act Transparency Statement|Sitemap|About US| Contact US: help@patsnap.com