Plate shape correction method during steel plate quenching based on model control
A model control, steel plate technology, applied in the direction of heat treatment process control, manufacturing tools, heat treatment equipment, etc., can solve problems such as warpage of steel plates, generation of temperature stress and structural stress, uneven cooling of steel plates, etc.
- Summary
- Abstract
- Description
- Claims
- Application Information
AI Technical Summary
Problems solved by technology
Method used
Image
Examples
Embodiment Construction
[0040] The technical solutions of the present invention will be further described below in conjunction with the accompanying drawings and embodiments.
[0041] refer to figure 1 , figure 1 A main flowchart 100 of the present invention is shown, including:
[0042] 101. Establish the surface structure distribution model of the steel plate, and output the fraction ratio of martensite on the upper and lower surfaces of the steel plate.
[0043] The warping amount and size parameters of the steel plate are obtained and input into the established distribution model of the steel plate surface structure, and the fraction ratio of martensite on the upper and lower surfaces of the steel plate is calculated and output.
[0044] 102. Establish a steel plate surface temperature model based on the steel plate surface structure distribution model.
[0045] 103. The steel plate surface temperature model outputs the surface temperature of the steel plate, and obtains the cooling rate ratio...
PUM
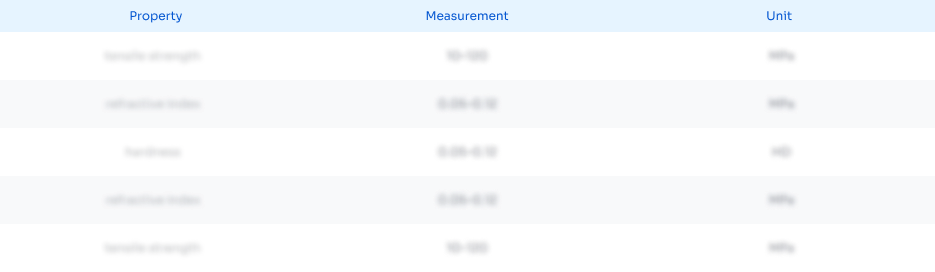
Abstract
Description
Claims
Application Information

- R&D
- Intellectual Property
- Life Sciences
- Materials
- Tech Scout
- Unparalleled Data Quality
- Higher Quality Content
- 60% Fewer Hallucinations
Browse by: Latest US Patents, China's latest patents, Technical Efficacy Thesaurus, Application Domain, Technology Topic, Popular Technical Reports.
© 2025 PatSnap. All rights reserved.Legal|Privacy policy|Modern Slavery Act Transparency Statement|Sitemap|About US| Contact US: help@patsnap.com