Aluminum alloy bodywork welding deformation flame correction method
An aluminum alloy vehicle body and welding deformation technology, which is applied in the field of flame adjustment of vehicle body welding deformation, can solve the problems such as the lack of success of cold orthosis and material damage, reduce the number of welding deformation adjustment, improve production efficiency, The effect of filling technical gaps
- Summary
- Abstract
- Description
- Claims
- Application Information
AI Technical Summary
Problems solved by technology
Method used
Examples
Embodiment 1
[0014] 1.5mm board tuning:
[0015] Step 1: Adjust the roasting gun to the middle blue fire length of 14 mm;
[0016] The second step: evenly heat the weld with a blue fire tip;
[0017] The third step: the heating rate is 90 cm / min;
[0018] The fourth step: the heating temperature is controlled at 120 degrees;
[0019] The fifth step: water cooling or air cooling.
Embodiment 2
[0021] 2.5mm plate tuning:
[0022] Step 1: Adjust the roasting gun to the middle blue fire length of 13mm;
[0023] The second step: evenly heat the weld with a blue fire tip;
[0024] The third step: the heating rate is 85 cm / min;
[0025] The fourth step: the heating temperature is controlled at 135 degrees;
[0026] The fifth step: water cooling or air cooling.
Embodiment 3
[0028] 4mm plate tuning:
[0029] Step 1: Adjust the roasting gun to the middle blue fire length of 13mm;
[0030] The second step: evenly heat the weld with a blue fire tip;
[0031] The third step: the heating rate is 80 cm / min;
[0032] The fourth step: the heating temperature is controlled at 140 degrees;
[0033] The fifth step: water cooling or air cooling.
PUM
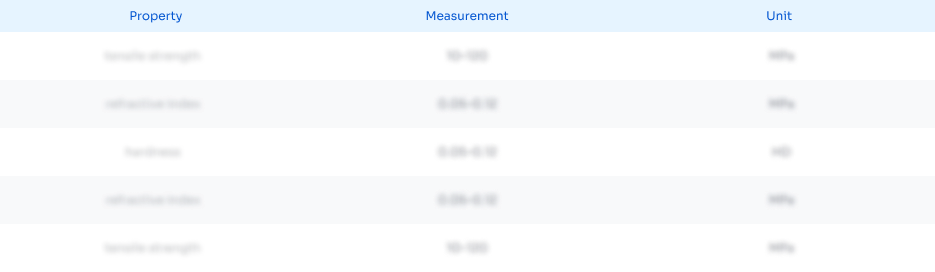
Abstract
Description
Claims
Application Information

- Generate Ideas
- Intellectual Property
- Life Sciences
- Materials
- Tech Scout
- Unparalleled Data Quality
- Higher Quality Content
- 60% Fewer Hallucinations
Browse by: Latest US Patents, China's latest patents, Technical Efficacy Thesaurus, Application Domain, Technology Topic, Popular Technical Reports.
© 2025 PatSnap. All rights reserved.Legal|Privacy policy|Modern Slavery Act Transparency Statement|Sitemap|About US| Contact US: help@patsnap.com