High-strength ceramsite propping agent and production method thereof
A production method and proppant technology, applied in the direction of earthwork drilling, production fluid, wellbore/well components, etc., can solve problems such as unstable product quality, failure to meet performance requirements, low pressure bearing capacity, etc., and achieve high pressure resistance Strength, improve the compressive strength, improve the effect of product quality
- Summary
- Abstract
- Description
- Claims
- Application Information
AI Technical Summary
Problems solved by technology
Method used
Image
Examples
Embodiment 1
[0020] Embodiment 1: High-strength ceramsite proppant and production method thereof
[0021] The composition of raw materials is shown in Table 1, in terms of weight percentage, that is, 80% of bauxite raw meal, 6% of barite, 0.1% of alum, 9.9% of iron oxide, and 4% of manganese ore powder. For raw material performance requirements, see the technical plan section.
[0022] Weigh each raw material, grind it into fine powder respectively, pass through a 320-mesh sieve, and the sieve rate is greater than 98.5%, mix and stir the raw materials evenly, under the unidirectional uniform rotation of the granulator, the mixture is continuously and evenly added to the granulator, and at the same time Atomize water vapor until the mixture forms round particles of different sizes; pass through a 18-30 mesh sieve, requiring a sieving rate of more than 80%, then rotate for 10-15 minutes, and pass through a 18-30 mesh sieve to obtain a semi-finished product; Lift the semi-finished product in...
Embodiment 2
[0023] Embodiment 2: The composition of raw materials is shown in Table 1, and the production method is basically the same as in Example 1, except that:
[0024] When the semi-finished product is fired in a rotary kiln, the temperature at the kiln head is 1350-1360°C, the temperature at the kiln tail is 310-320°C, and the finished product is obtained after firing for 6 hours.
Embodiment 3
[0025] Embodiment 3: The raw material composition is shown in Table 1, and the production method is basically the same as in Example 1, the difference being:
[0026] When the semi-finished product is fired in a rotary kiln, the temperature at the kiln head is 1380-1400°C, and the temperature at the end of the kiln is 300-310°C. After firing for 7 hours, the finished product is obtained from the kiln.
PUM
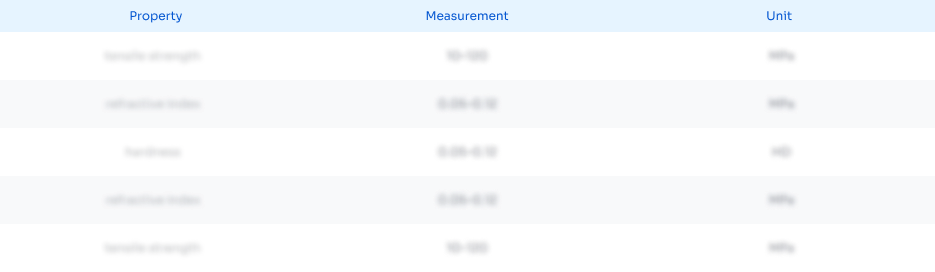
Abstract
Description
Claims
Application Information

- R&D
- Intellectual Property
- Life Sciences
- Materials
- Tech Scout
- Unparalleled Data Quality
- Higher Quality Content
- 60% Fewer Hallucinations
Browse by: Latest US Patents, China's latest patents, Technical Efficacy Thesaurus, Application Domain, Technology Topic, Popular Technical Reports.
© 2025 PatSnap. All rights reserved.Legal|Privacy policy|Modern Slavery Act Transparency Statement|Sitemap|About US| Contact US: help@patsnap.com