Non-contact three-dimensional optical measuring head and method for in-situ measurement of numerical control machine
A three-dimensional optical, numerically controlled machine tool technology, used in measuring/indicating equipment, metal processing mechanical parts, metal processing equipment, etc., can solve the problems of measurement force system error, measurement efficiency influence, damage to the surface of the workpiece, etc., to achieve high precision, improve The effect of equipment utilization and low cost
- Summary
- Abstract
- Description
- Claims
- Application Information
AI Technical Summary
Problems solved by technology
Method used
Image
Examples
Embodiment Construction
[0024] In this embodiment, the vertical CNC milling machine XD30A of Dalian Machine Tool Group and the FANUC 0i Mate CNC system are used.
[0025] see figure 1 , The in-situ measurement system for CNC machine tools in this embodiment consists of a vertical CNC milling machine, a non-contact three-dimensional optical probe, an industrial computer and visual in-situ measurement software. The non-contact three-dimensional optical probe is installed on the Z-axis of the main body of the machine tool, and the Z-axis coordinate value of the non-contact three-dimensional optical probe is defined as the Z-axis coordinate value of the vertical CNC milling machine. The input end of the servo system is connected to the CNC system, and the output of the servo system is The end is connected with the motor of the vertical CNC milling machine, the CNC system drives the motor to rotate through the servo system, the CNC system is connected with the non-contact 3D optical probe, and the industr...
PUM
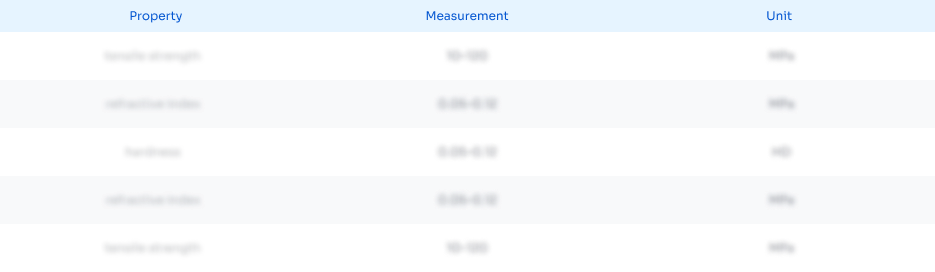
Abstract
Description
Claims
Application Information

- Generate Ideas
- Intellectual Property
- Life Sciences
- Materials
- Tech Scout
- Unparalleled Data Quality
- Higher Quality Content
- 60% Fewer Hallucinations
Browse by: Latest US Patents, China's latest patents, Technical Efficacy Thesaurus, Application Domain, Technology Topic, Popular Technical Reports.
© 2025 PatSnap. All rights reserved.Legal|Privacy policy|Modern Slavery Act Transparency Statement|Sitemap|About US| Contact US: help@patsnap.com