Hot blast stove for refining iron and improved construction process
A construction process and hot blast stove technology, which are used in the field of metallurgical industry production furnaces and iron production hot blast stoves, can solve the cracks of metal burners and hot blast stove shell materials, the short service life of the hot blast stove dome, and the external burner. 4. High temperature problem, to reduce maintenance workload, eliminate potential safety hazards, and stabilize wind temperature
- Summary
- Abstract
- Description
- Claims
- Application Information
AI Technical Summary
Problems solved by technology
Method used
Image
Examples
specific Embodiment approach
[0039] The regenerator inside the hot blast stove of the present invention adopts checker bricks. In order to adapt to the downward movement of the high-temperature combustion zone 6, the material properties of the top part of the regenerator and the wall material have been improved, and the structure and equipment below the hot air outlet have not been changed.
[0040] The hot blast stove is equipped with a nitrogen purging system and a nitrogen purging system control device.
[0041] Improve supporting air and gas pipelines.
[0042] The nitrogen purging system control device includes a regulating valve and an electric control part.
[0043] The invention structurally solves the requirements of high wind temperature on the vault stability and longevity of the top-fired hot blast stove; eliminates the heavy and dangerous maintenance work such as cracking of the external burner and running wind, greatly improves the operation safety, and greatly improves the operation safety...
PUM
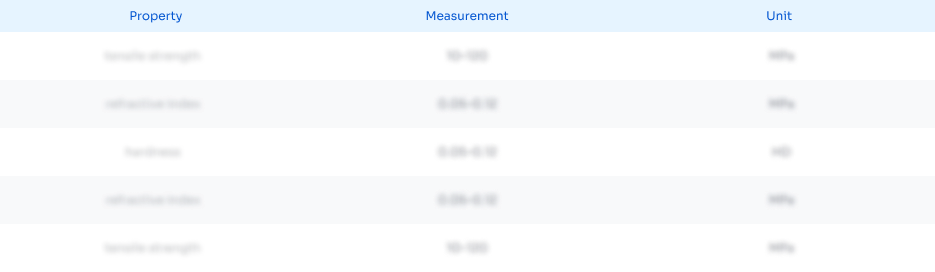
Abstract
Description
Claims
Application Information

- R&D Engineer
- R&D Manager
- IP Professional
- Industry Leading Data Capabilities
- Powerful AI technology
- Patent DNA Extraction
Browse by: Latest US Patents, China's latest patents, Technical Efficacy Thesaurus, Application Domain, Technology Topic, Popular Technical Reports.
© 2024 PatSnap. All rights reserved.Legal|Privacy policy|Modern Slavery Act Transparency Statement|Sitemap|About US| Contact US: help@patsnap.com