Packaging method for flip LED chips
A technology of LED chip and packaging method, which is applied in the direction of electrical components, circuits, semiconductor devices, etc., can solve the problems of waste, wire collapse, low coating efficiency, etc., achieve the improvement of color zone completion rate, improve product yield, coating The effect of uniform thickness
- Summary
- Abstract
- Description
- Claims
- Application Information
AI Technical Summary
Problems solved by technology
Method used
Image
Examples
Embodiment Construction
[0023] In order to describe the technical content, structural features, achieved goals and effects of the present invention in detail, the following will be described in detail in conjunction with the embodiments and accompanying drawings.
[0024] Since the specific structure of the flip-chip LED chip is already in the prior art, the Chinese invention patent with the publication number CN100380694C and the invention name "A Flip-chip LED Packaging Method" has detailed introductions, so the specific embodiment of the present invention is only for flip-chip LED chips. The improved part of the LED chip packaging method is introduced.
[0025] As an embodiment of the packaging method of the flip-chip LED chip of the present invention, please refer to FIG. 3, at least including the following steps:
[0026] (a) coating the phosphor 4 on the surface of the light-emitting surface of the LED chip 2 by screen printing, and baking and curing the phosphor 4;
[0027] (b) Fixing the LED...
PUM
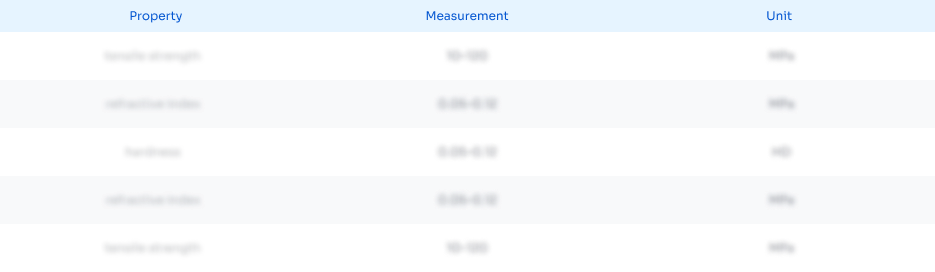
Abstract
Description
Claims
Application Information

- R&D
- Intellectual Property
- Life Sciences
- Materials
- Tech Scout
- Unparalleled Data Quality
- Higher Quality Content
- 60% Fewer Hallucinations
Browse by: Latest US Patents, China's latest patents, Technical Efficacy Thesaurus, Application Domain, Technology Topic, Popular Technical Reports.
© 2025 PatSnap. All rights reserved.Legal|Privacy policy|Modern Slavery Act Transparency Statement|Sitemap|About US| Contact US: help@patsnap.com