Thin-film magnetoresistive sensor
A magnetoresistive sensor and thin film technology, applied in the sensor field, can solve the problems affecting sensor performance, limiting chip design, limited bias magnetic field, etc., to achieve the effects of improving measurement accuracy and linearity process, low manufacturing cost, and high corresponding frequency
- Summary
- Abstract
- Description
- Claims
- Application Information
AI Technical Summary
Problems solved by technology
Method used
Image
Examples
Embodiment Construction
[0017] The present invention will be further described below in conjunction with specific drawings and embodiments.
[0018] Such as figure 1 Shown: the present invention includes a seed layer 1, a first nonmagnetic pinned layer 2, a first magnetic pinned layer 3, a nonmagnetic spacer layer 4, a second magnetic pinned layer 5, a second nonmagnetic pinned layer 6 and protective layer 7.
[0019] Such as figure 1 As shown, the seed layer 1 is provided with a first non-magnetic pinning layer 2, and the first non-magnetic pinning layer 2 is provided with a first magnetic pinned layer 3; Layer 3 and the first non-magnetic pinning layer 2 form a reference layer, and generate a first exchange coupling field; the direction of magnetic moment of the reference layer generating the first exchange coupling field is shown in 8 . A non-magnetic spacer 4 is disposed on the first magnetic pinned layer 3, and the material of the non-magnetic spacer 4 can be Cu, AlO, MgO, HFO, ZrO or TaO. T...
PUM
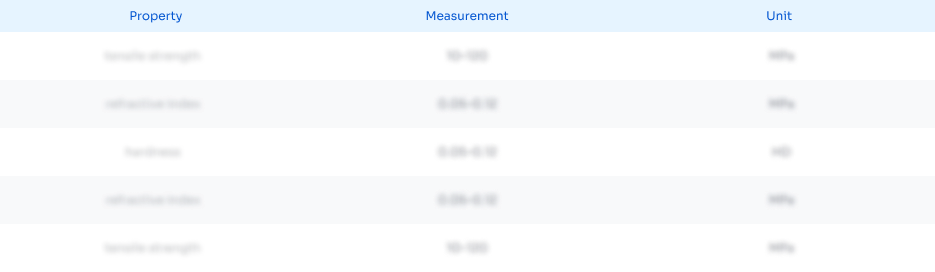
Abstract
Description
Claims
Application Information

- R&D
- Intellectual Property
- Life Sciences
- Materials
- Tech Scout
- Unparalleled Data Quality
- Higher Quality Content
- 60% Fewer Hallucinations
Browse by: Latest US Patents, China's latest patents, Technical Efficacy Thesaurus, Application Domain, Technology Topic, Popular Technical Reports.
© 2025 PatSnap. All rights reserved.Legal|Privacy policy|Modern Slavery Act Transparency Statement|Sitemap|About US| Contact US: help@patsnap.com