Production technique for extracting ammonium thiosulfate and ammonium thiocyanate from desulfurization waste liquor
A technology of ammonium thiosulfate and desulfurization waste liquid, which is applied in the direction of thiosulfate/dithionite/polythionate, thiocyanate, etc., which can solve the problems that the products are difficult to meet the industrial requirements and reduce emissions And environmental pollution, improve the effect of economic benefits
- Summary
- Abstract
- Description
- Claims
- Application Information
AI Technical Summary
Problems solved by technology
Method used
Examples
Embodiment 1
[0020] Take 500ml of desulfurization waste liquid in the HPF desulfurization production process of the coking plant, settle for 12 hours, filter to obtain 1.2g of sulfur, add 2g of activated carbon to the filtrate, heat and stir for 3 hours, filter to remove the activated carbon. Filtrate is added in the 1000ml three-necked flask that has stirrer, thermometer, under 5mmHg pressure, when underpressure distillation to temperature 80 ℃, filter while hot, filter cake oven dry, obtain ammonium thiosulfate 23.1g, content is 98.3%. Continue vacuum distillation until the filtrate is evaporated to dryness, add 400ml of methanol and 50ml of ethylenediamine mixture, reflux for 30 minutes, heat filter, and dry the filter cake to obtain 35.3g of ammonium thiosulfate with a content of 98.1%. The filtrate was pressurized to 7mmHg, and when 250ml of mixed solvent was steamed out by vacuum distillation, the heating was stopped, and the steamed mixed solvent was recovered and recycled, and the f...
Embodiment 2
[0022] Take 500ml of desulfurization waste liquid in the HPF desulfurization production process of the coking plant, settle for 12 hours, filter to obtain 1.1g of sulfur, add 3g of activated clay to the filtrate, heat and stir for 3 hours, filter to remove the activated clay. The filtrate was added in a 1000ml three-necked flask with a stirrer and a thermometer. Under 5mmHg pressure, when the pressure was distilled to a temperature of 80°C, it was filtered while it was hot, and the filter cake was dried to obtain 23.8g of ammonium thiosulfate, with a content of 98.4%. Continue vacuum distillation until the filtrate is evaporated to dryness, add 570ml of ethanol and 30ml of ethylenediamine mixture, reflux for 30 minutes, heat filter, and dry the filter cake to obtain 34.9g of ammonium thiosulfate with a content of 98.2%. The filtrate is pressurized to 7mmHg, and when decompression distillation steams 250ml mixed solvent, stop heating, steams mixed solvent and recycles, and filtr...
Embodiment 3
[0024] Take 500ml of desulfurization waste liquid in the HPF desulfurization production process of the coking plant, settle for 12 hours, filter to obtain 1.1g of sulfur, add 5g of activated clay to the filtrate, heat and stir for 3 hours, filter to remove the activated clay. Filtrate is added in the 1000ml three-necked flask that has stirrer, thermometer, under 5mmHg pressure, when underpressure distillation to temperature 80 ℃, filter while hot, filter cake oven dry, obtain ammonium thiosulfate 24.3g, content is 98.5%. Continue vacuum distillation until the filtrate is evaporated to dryness, add 450ml of acetonitrile and 50ml of ethylenediamine mixture, reflux for 30 minutes, heat filter, and dry the filter cake to obtain 34.9g of ammonium thiosulfate with a content of 98.4%. The filtrate is pressurized to 7mmHg, and when decompression distillation steams 250ml mixed solvent, stop heating, steams mixed solvent and recycles, and filtrate is cooled to room temperature, crystall...
PUM
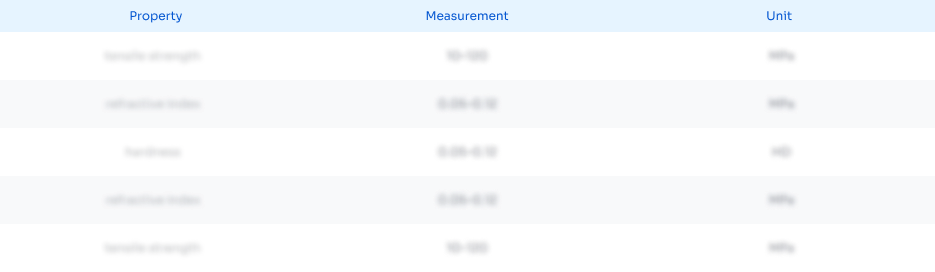
Abstract
Description
Claims
Application Information

- R&D
- Intellectual Property
- Life Sciences
- Materials
- Tech Scout
- Unparalleled Data Quality
- Higher Quality Content
- 60% Fewer Hallucinations
Browse by: Latest US Patents, China's latest patents, Technical Efficacy Thesaurus, Application Domain, Technology Topic, Popular Technical Reports.
© 2025 PatSnap. All rights reserved.Legal|Privacy policy|Modern Slavery Act Transparency Statement|Sitemap|About US| Contact US: help@patsnap.com