Manufacturing method of oriented film and LCD panel
A technology of liquid crystal display panels and manufacturing methods, applied in the direction of nonlinear optics, instruments, optics, etc., can solve problems such as lowering the qualified rate, increasing production costs, and circuit damage on the substrate, so as to avoid static electricity problems, simplify the manufacturing process, and pass rate-enhancing effect
- Summary
- Abstract
- Description
- Claims
- Application Information
AI Technical Summary
Problems solved by technology
Method used
Image
Examples
Embodiment Construction
[0023] A method for manufacturing an alignment film for a liquid crystal display panel and a method for manufacturing a liquid crystal display panel according to a preferred embodiment of the present invention will be described below with reference to related drawings, wherein the same components will be described with the same symbols.
[0024] figure 2 It is a flow chart of a method for manufacturing a liquid crystal display panel in a preferred embodiment of the present invention. In this embodiment, the manufacturing method mainly includes step S11 to step S16. The following fit Figure 3A to Figure 3D The manufacturing method of this example will be described.
[0025] Such as figure 2 and Figure 3A As shown, step S11 is to form a curable material layer 21 on the substrate 22, wherein the curable material has a side chain structure A1. Step S12 is to form another curable material layer 26 on another substrate 23 , wherein the other curable material has another sid...
PUM
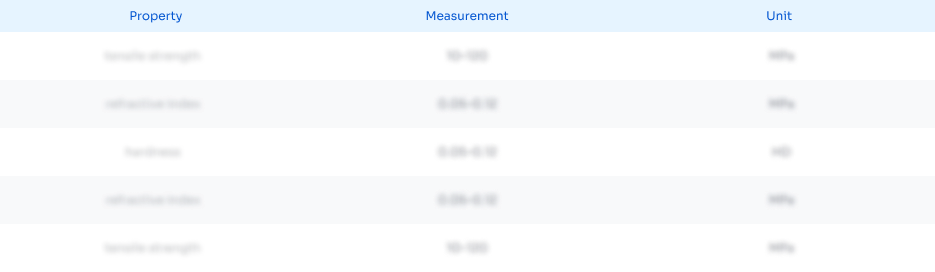
Abstract
Description
Claims
Application Information

- R&D Engineer
- R&D Manager
- IP Professional
- Industry Leading Data Capabilities
- Powerful AI technology
- Patent DNA Extraction
Browse by: Latest US Patents, China's latest patents, Technical Efficacy Thesaurus, Application Domain, Technology Topic, Popular Technical Reports.
© 2024 PatSnap. All rights reserved.Legal|Privacy policy|Modern Slavery Act Transparency Statement|Sitemap|About US| Contact US: help@patsnap.com