Steel tube multiple-wire internal welding machine nose
An internal welding machine and steel pipe technology, applied in auxiliary devices, welding equipment, auxiliary welding equipment, etc., can solve the problems of large wire feeding resistance, increased wire feeding resistance, and difficult bending of wire feeding hoses, and achieves unique design, Novel structure, solving the effect of small hole diameter multi-wire large straight seam internal welding
- Summary
- Abstract
- Description
- Claims
- Application Information
AI Technical Summary
Problems solved by technology
Method used
Image
Examples
Embodiment Construction
[0017] Such as figure 1 As shown, the head device of the steel pipe multi-wire internal welding machine includes a flux cylinder 4, a wire feeding panel 11, a wire guide wheel 10 and a contact tip 5, and several guide wheels 10 are regularly distributed on the front of the wire feeding panel 11, forming A plurality of guide wire channels, on the back of the wire feed panel 11 is lined with a connection back plate 9, the wire guide wheel 10 passes through the wire feed panel 11 and is fixed to the connection back plate 9; a guide wire joint is installed above the wire feed panel 11 2. A nozzle plate 8 is connected below the wire feeding panel 11, and a plurality of nozzle blocks 7 are fixed on the nozzle plate 8, and each nozzle block 7 is connected with a conductive tip 5 by screw connection, each The upper port of the contact tip 5 is in contact with the guide wire channel; in addition, a flux cartridge 4 is installed on the wire feeding panel 11 , and the outlet of the flux ...
PUM
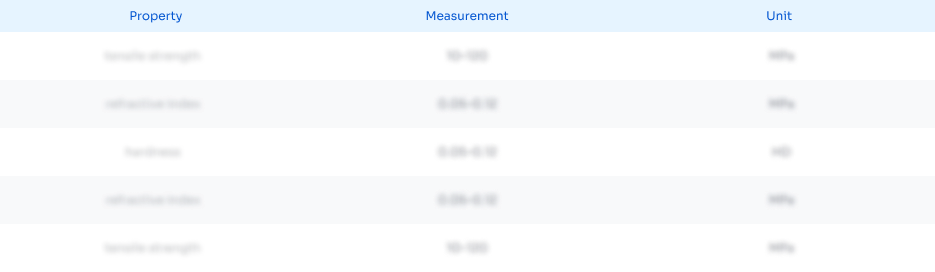
Abstract
Description
Claims
Application Information

- Generate Ideas
- Intellectual Property
- Life Sciences
- Materials
- Tech Scout
- Unparalleled Data Quality
- Higher Quality Content
- 60% Fewer Hallucinations
Browse by: Latest US Patents, China's latest patents, Technical Efficacy Thesaurus, Application Domain, Technology Topic, Popular Technical Reports.
© 2025 PatSnap. All rights reserved.Legal|Privacy policy|Modern Slavery Act Transparency Statement|Sitemap|About US| Contact US: help@patsnap.com