Precast composite outer insulated wall plate and manufacturing method thereof
A technology of external thermal insulation and wall panels, applied in the processing of building materials, building materials, construction, etc., can solve the problems of unguaranteed construction quality, high construction cost, environmental pollution, etc., to save the renovation period, reduce construction waste, simplify The effect of the construction process
- Summary
- Abstract
- Description
- Claims
- Application Information
AI Technical Summary
Problems solved by technology
Method used
Image
Examples
Embodiment 1
[0067] Embodiment one sees Figure 1-4 As shown, this kind of prefabricated composite external thermal insulation wallboard has a structural layer 1, an insulating layer 3 and a protective layer 2 in sequence from the inside to the outside. There is a steel cage in the structural layer, and the thermal insulation layer 3 is extruded polystyrene foam. The plastic plate, the concrete of the protective layer 2 has a reinforced mesh sheet, and the structural layer 1, the thermal insulation layer 3 and the protective layer 2 are interspersed and anchored together by the connectors 5 distributed in a point shape. The distribution of the connectors can be found in Figure 11 . The left and right edges of the protective layer 2 and the thermal insulation layer 3 protrude from the structural layer 1, and the lower edge of the protective layer 2 extends downwards to form a protrusion 7, and the tops of the protective layer 2 and the thermal insulation layer 3 protrude upwards from the s...
Embodiment 2
[0074] Embodiment two see Figure 5 , the outer surface of the protective layer 2 is connected with an outer decorative layer 4, and the outer decorative layer 4 is a face brick, a paint or a decorative board.
[0075] When the outer side of the protective layer does not need an outer decorative layer, or although an outer decorative layer is required, but the outer decorative layer is not a facing brick, there are two methods for making the prefabricated composite outer thermal insulation wallboard.
[0076] The first kind: step 1, assembling formwork; Step 2, place reinforcement cage, reinforcement ring 15 and internal thread sleeve 9 on the base form, comprise horizontal tie reinforcement 14, vertical connection reinforcement 10 on the reinforcement cage, reinforce reinforcement sleeve 6 is fixedly connected with the reinforcement cage of the structural layer, and the short grouting pipe 13 and the short grouting pipe 11 are fixedly connected with the steel bar sleeve 6; St...
PUM
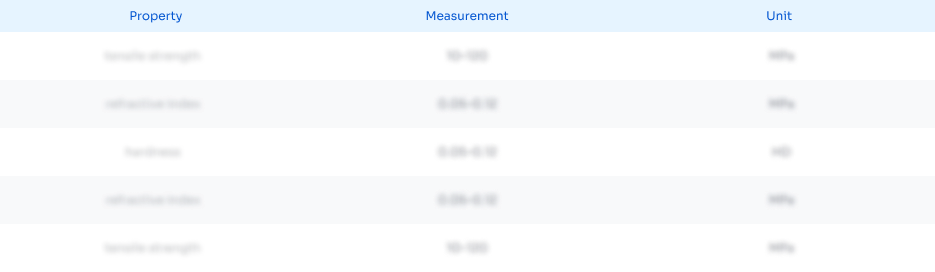
Abstract
Description
Claims
Application Information

- R&D Engineer
- R&D Manager
- IP Professional
- Industry Leading Data Capabilities
- Powerful AI technology
- Patent DNA Extraction
Browse by: Latest US Patents, China's latest patents, Technical Efficacy Thesaurus, Application Domain, Technology Topic, Popular Technical Reports.
© 2024 PatSnap. All rights reserved.Legal|Privacy policy|Modern Slavery Act Transparency Statement|Sitemap|About US| Contact US: help@patsnap.com