Full liquefying separation process for air-containing coal bed gas
A liquefaction separation and coal bed gas technology, applied in liquefaction, refrigeration, liquefaction, solidification, etc., can solve problems such as waste, complicated process flow, and failure to achieve complete separation of liquefied natural gas, and achieve the effect of reducing the number of equipment and simplifying process steps
- Summary
- Abstract
- Description
- Claims
- Application Information
AI Technical Summary
Problems solved by technology
Method used
Image
Examples
Embodiment 1
[0051] This embodiment provides a fully liquefied separation process for air-containing coalbed methane. The hydrocarbon-oxygen separation equipment used in the process is a double-layer hydrocarbon-oxygen separation tower. The double-layer hydrocarbon-oxygen separation tower includes an upper tower and a lower tower, and , a condensing evaporator is arranged between the upper tower and the lower tower; the full liquefaction separation process comprises the following steps:
[0052] The compressed and purified air-containing coalbed methane is cooled and passed into the middle of the lower tower, through the heating at the bottom of the lower tower and the condensation on the condensation side of the condensing evaporator, liquid hydrocarbons are obtained at the bottom of the lower tower, and the mixed gas separated from the hydrocarbons is After throttling, it enters the top of the upper tower, or the mixed gas separated from hydrocarbons enters the middle of the nitrogen sepa...
Embodiment 2
[0056] This embodiment provides a full liquefaction separation process for air-containing coalbed methane, wherein the full liquefaction separation equipment used is such as figure 1 shown.
[0057] The full liquefaction separation equipment includes a compression purification system 1, a cooling system 2 and a liquefaction separation system, wherein the compression purification system 1 is used to compress and purify the air-containing coalbed methane, and the cooling system 2 is used to provide refrigeration and can process part of the product The cold energy is recovered, both of which can adopt the system commonly used in this field;
[0058] The liquefaction separation system includes a double-layer hydrocarbon-oxygen separation tower and a nitrogen separation tower 304. The double-layer hydrocarbon-oxygen separation tower is composed of an upper tower 301 and a lower tower 302, and a condensation evaporator 303 is arranged between the upper tower 301 and the lower tower ...
Embodiment 3
[0067] This embodiment provides a full liquefaction separation process for air-containing coalbed methane, wherein the full liquefaction separation equipment used is such as figure 2 shown.
[0068] In this full liquefaction separation equipment, the cooling system includes a compressor 201, an air cooler 202, a gas-liquid separation tank 203, a compressor 204, an air cooler 205, a gas-liquid separation tank 206, a first Cold box 207 and second cold box 208, a section of gas-liquid separation tank 203 has an inlet, a top outlet and a bottom outlet, wherein:
[0069] One section of compressor 201, one section of air cooler 202, the inlet of one section of gas-liquid separation tank 203, the bottom outlet of one section of separation gas-liquid tank 203, the first cold box (second flow channel) 207, the first JT valve 209 and the first cooling Boxes (third runners) 207 are connected in sequence to form a high-temperature cycle;
[0070] One-stage compressor 201, one-stage air...
PUM
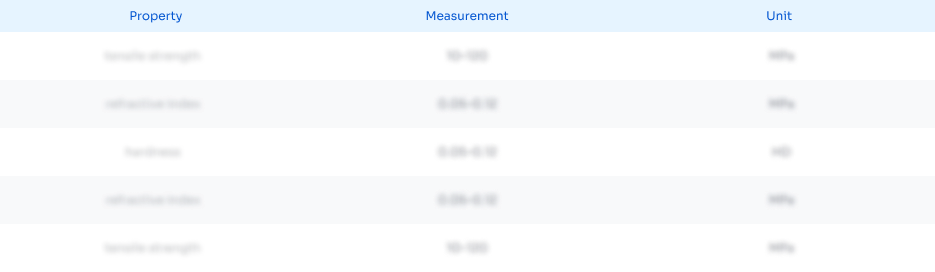
Abstract
Description
Claims
Application Information

- R&D
- Intellectual Property
- Life Sciences
- Materials
- Tech Scout
- Unparalleled Data Quality
- Higher Quality Content
- 60% Fewer Hallucinations
Browse by: Latest US Patents, China's latest patents, Technical Efficacy Thesaurus, Application Domain, Technology Topic, Popular Technical Reports.
© 2025 PatSnap. All rights reserved.Legal|Privacy policy|Modern Slavery Act Transparency Statement|Sitemap|About US| Contact US: help@patsnap.com