Method for preparing chloroethylene by catalytic reforming
A technology for catalytic reforming and vinyl chloride, applied in chemical instruments and methods, preparation of halogenated hydrocarbons, physical/chemical process catalysts, etc., can solve the problems of low raw material cost, high equipment requirements, and inability to solve mercury, so as to reduce synthesis Combined with refining process, solving the problem of high temperature energy consumption, and solving the effect of mercury pollution
- Summary
- Abstract
- Description
- Claims
- Application Information
AI Technical Summary
Problems solved by technology
Method used
Examples
Embodiment 1
[0020] Dissolve 1g of barium chloride in 150ml of water, add 100g of activated carbon, mix well, and dry at 180°C to prepare the catalyst. Mix acetylene and ethylene dichloride steam at a ratio of 1:4, and pass it into a reactor equipped with a catalyst supported by activated carbon for reaction. The reaction temperature is controlled at 320 ° C, and the reaction time is 5 minutes. After the reaction, the gas is cooled to room temperature. The liquid unreacted ethylene dichloride is separated first, and then the remaining gas is frozen and compressed to obtain liquid vinyl chloride. Calculated by acetylene, the primary conversion rate is over 70%, and the selectivity of vinyl chloride is over 90%.
Embodiment 2
[0022] Dissolve 5g of barium chloride in 150ml of water, add 100g of activated carbon, mix well, and dry at 150°C to obtain the catalyst. Mix acetylene and ethylene dichloride steam at a ratio of 1:3, and pass it into a reactor equipped with a catalyst supported by activated carbon for reaction. The reaction temperature is controlled at 300°C, and the reaction time is 10 minutes. After the reaction, the gas is cooled to room temperature. The liquid unreacted ethylene dichloride is separated first, and then the remaining gas is frozen and compressed to obtain liquid vinyl chloride. Calculated by acetylene, the primary conversion rate is over 70%, and the selectivity of vinyl chloride is over 92%.
Embodiment 3
[0024] Dissolve 10g of barium chloride in 150ml of water, add 100g of activated carbon, mix well and dry at 250°C to obtain the catalyst. Mix acetylene and ethylene dichloride vapor at a ratio of 1:2, and pass it into a reactor equipped with a catalyst supported by activated carbon for reaction. The reaction temperature is controlled at 280°C, and the reaction time is 2 minutes. After the reaction, the gas is cooled to room temperature. The liquid unreacted ethylene dichloride is separated first, and then the remaining gas is frozen and compressed to obtain liquid vinyl chloride. Calculated by acetylene, the primary conversion rate is over 70%, and the selectivity of vinyl chloride is over 95%.
PUM
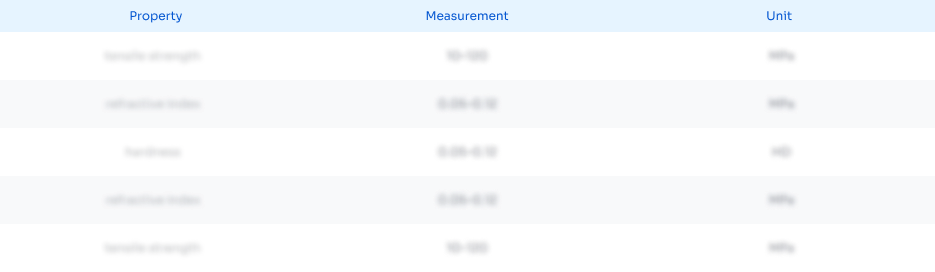
Abstract
Description
Claims
Application Information

- Generate Ideas
- Intellectual Property
- Life Sciences
- Materials
- Tech Scout
- Unparalleled Data Quality
- Higher Quality Content
- 60% Fewer Hallucinations
Browse by: Latest US Patents, China's latest patents, Technical Efficacy Thesaurus, Application Domain, Technology Topic, Popular Technical Reports.
© 2025 PatSnap. All rights reserved.Legal|Privacy policy|Modern Slavery Act Transparency Statement|Sitemap|About US| Contact US: help@patsnap.com