Process for separating and recovering butyl acetate and butyl alcohol in wastewater by using azeotropic rectification
A technology for the separation and recovery of butyl acetate, applied in the m-HSAD process field, can solve the problems of high energy consumption, separation and refining, etc., and achieve the effects of short process route, reduced energy consumption, and low investment
- Summary
- Abstract
- Description
- Claims
- Application Information
AI Technical Summary
Problems solved by technology
Method used
Image
Examples
Embodiment 1
[0020] With butanol 0.1% (wt), butyl acetate 1% (wt), water 97.9% (wt), organic residue (or other high boiling matter) 1% (wt) flow rate is the waste water of 0.125 tons / hour, It is preheated to 45°C by heat exchanger H-01, then heated to 80°C by heat exchanger H-02, and then enters the first rectification tower T-01. The theoretical plate number of the first rectification tower T-01 is 28 block, the tower diameter is 0.3 meters, the operating pressure is normal pressure, and the tower kettle is heated by steam. The condensate of the steam at the top of the first rectification tower T-01 after heat exchange enters the phase separation tank S1, and the heavy phase refluxes. The temperature at the top of the rectification tower T-01 is 85°C, the temperature at the bottom of the tower is 100°C, and the bottom of the tower can obtain pure water and organic residues (or other high boiling substances). The light phase is extracted and enters the second rectification tower T-02. The ...
Embodiment 2
[0022] With butanol 7% (wt), butyl acetate 5% (wt), water 85% (wt), the flow of organic residue (or other high boiler) 3% (wt) is the waste water of 0.3 ton / hour through Heat exchanger H-01 is preheated to 50°C, then heated to 85°C by heat exchanger H-02, and then enters the first rectification tower T-01, the number of theoretical plates of the first rectification tower T-01 is 30 , the tower diameter is 0.6 meters, the operating pressure is normal pressure, the tower kettle is heated by steam, the condensate of the steam at the top of the first rectification tower T-01 after heat exchange enters the phase separation tank S1, the heavy phase is refluxed, and the first rectification The temperature at the top of the distillation tower T-01 is 90°C, and the temperature at the bottom of the tower is 103°C, and the bottom of the tower can obtain pure water and organic residues (or other high boilers). The light phase is extracted and enters the second rectification tower T-02. Th...
Embodiment 3
[0024] With butanol 5% (wt), butyl acetate 3% (wt), water 90% (wt), the flow of organic residue (or other high boiler) 2% (wt) is the waste water of 1.0 tons / hour through Heat exchanger H-01 is preheated to 52°C, then heated to 90°C by heat exchanger H-02, and then enters the first rectification tower T-01, the number of theoretical plates of the first rectification tower T-01 is 32 , the tower diameter is 0.8 meters, the operating pressure is normal pressure, the tower kettle is heated by steam, the condensate of the steam at the top of the first rectification tower T-01 after heat exchange enters the phase separation tank S1, the heavy phase is refluxed, and the first rectification The temperature at the top of the distillation tower T-01 is 95° C., and the temperature at the bottom of the tower is 105° C. The bottom of the tower can obtain pure water and organic residues (or other high boilers). The light phase is extracted and enters the second rectification tower T-02. Th...
PUM
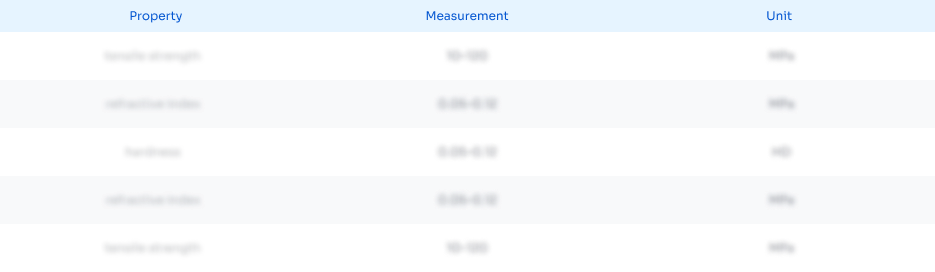
Abstract
Description
Claims
Application Information

- R&D
- Intellectual Property
- Life Sciences
- Materials
- Tech Scout
- Unparalleled Data Quality
- Higher Quality Content
- 60% Fewer Hallucinations
Browse by: Latest US Patents, China's latest patents, Technical Efficacy Thesaurus, Application Domain, Technology Topic, Popular Technical Reports.
© 2025 PatSnap. All rights reserved.Legal|Privacy policy|Modern Slavery Act Transparency Statement|Sitemap|About US| Contact US: help@patsnap.com