Transparent ABS material and preparation method thereof
An ABS material and transparent technology, applied in the field of transparent ABS materials and its preparation, can solve the problems of easy accumulation of large static charges, affecting the appearance of products, catastrophic accidents, etc., achieve excellent transparency, broad application prospects, and good chemical resistance Effect
- Summary
- Abstract
- Description
- Claims
- Application Information
AI Technical Summary
Problems solved by technology
Method used
Examples
Embodiment 1
[0024] Dry the ABS raw material at 80°C for 3 hours, and weigh the raw material according to the following weight percentage: ABS 90%, main antistatic agent 5%, auxiliary antistatic agent 3%, high temperature antioxidant 2%;
[0025] First pre-mix the main antistatic agent, auxiliary antistatic agent and high-temperature antioxidant for 2-3 minutes, then add the dried ABS and pre-mixed materials into the high-speed batch mixer, and mix for 5 to 8 minutes;
[0026] Put the mixed material into a single-screw machine to melt, extrude and granulate. The process is: single-screw first stage temperature 170-280°C, second stage temperature 180-190°C, third stage temperature 190-200°C, mold temperature 30-60°C, residence time 1-2 minutes, pressure 10-15MPa.
Embodiment 2
[0028] Dry the ABS raw material at 80°C for 3 hours, and weigh the raw material according to the following weight percentage: ABS 93%, main antistatic agent 5%, auxiliary antistatic agent 1%, high temperature antioxidant 1%;
[0029] First pre-mix the main antistatic agent, auxiliary antistatic agent and high-temperature antioxidant for 2-3 minutes, then add the dried ABS and pre-mixed materials into the high-speed batch mixer, and mix for 5 to 8 minutes;
[0030] Put the mixed material into a single-screw machine to melt, extrude and granulate. The process is: single-screw first stage temperature 170-280°C, second stage temperature 180-190°C, third stage temperature 190-200°C, mold temperature 30-60°C, residence time 1-2 minutes, pressure 10-15MPa.
Embodiment 3
[0032] Dry the ABS raw material at 80°C for 3 hours, and weigh the raw material according to the following weight percentage: ABS 95%, main antistatic agent 2%, auxiliary antistatic agent 2%, high temperature antioxidant 1%;
[0033] First pre-mix the main antistatic agent, auxiliary antistatic agent and high-temperature antioxidant for 2-3 minutes, then add the dried ABS and pre-mixed materials into the high-speed batch mixer, and mix for 5 to 8 minutes;
[0034] Put the mixed material into a single-screw machine to melt, extrude and granulate. The process is: single-screw first stage temperature 170-280°C, second stage temperature 180-190°C, third stage temperature 190-200°C, mold temperature 30-60°C, residence time 1-2 minutes, pressure 10-15MPa.
[0035] Performance testing and characterization are based on ASTM related standards; the test conditions are 23°C, 53% relative humidity.
[0036] Tensile Strength / Elongation at Break: ASTM D638;
[0037] Flexural strength / flex...
PUM
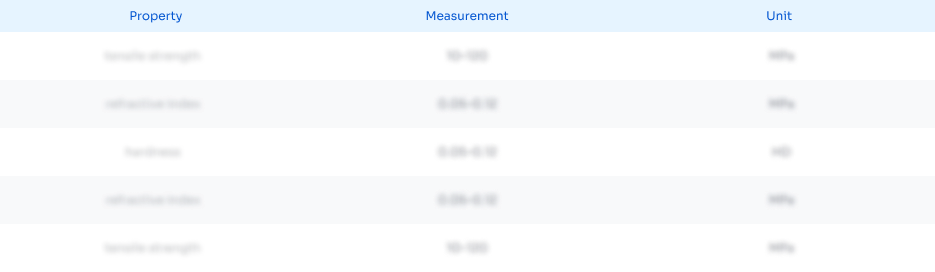
Abstract
Description
Claims
Application Information

- R&D Engineer
- R&D Manager
- IP Professional
- Industry Leading Data Capabilities
- Powerful AI technology
- Patent DNA Extraction
Browse by: Latest US Patents, China's latest patents, Technical Efficacy Thesaurus, Application Domain, Technology Topic, Popular Technical Reports.
© 2024 PatSnap. All rights reserved.Legal|Privacy policy|Modern Slavery Act Transparency Statement|Sitemap|About US| Contact US: help@patsnap.com