Manufacturing method of nickel-plated natural garnet anti-abrasion material
A technology of wear-resistant material and manufacturing method, which is applied in the manufacturing field of nickel-plated natural garnet wear-resistant materials, can solve the problems of poor wear resistance of natural abrasives, etc., and achieves the effects of increasing strength, simple process and improved wear resistance.
- Summary
- Abstract
- Description
- Claims
- Application Information
AI Technical Summary
Problems solved by technology
Method used
Examples
Embodiment 1
[0016] A kind of manufacture method of nickel-plated natural garnet wear-resistant material, it comprises the following steps:
[0017] a. Weigh 10kg of natural garnet matrix powder, the matrix powder is the standard particle size of No. 24, weigh 10g of nickel nitrate and 10g of borax, first dissolve borax in 100g of water and heat to 100°C, stir for 5 minutes , and then add nickel nitrate under stirring conditions to make a plating solution;
[0018] b. Put the natural garnet matrix powder into the stirring pot, add the plating solution in step a, and stir for 5 minutes;
[0019] c. Put the natural garnet matrix powder mixed with the plating solution in step b into an oven, and dry at 120° C. for 30 minutes;
[0020] d. Place the dried natural garnet matrix powder in step c in a kiln, raise the temperature to 750° C., keep it warm for 20 minutes, cool it down to normal temperature naturally, and sieve the cooled matrix powder.
Embodiment 2
[0022] A kind of manufacture method of nickel-plated natural garnet wear-resistant material, it comprises the following steps:
[0023] a. take by weighing 10kg natural garnet matrix powder, matrix powder is the mixture of the standard particle size number of No. 70 of 5kg and the standard particle size number of No. 80 of 5kg, take by weighing the nickel nitrate of 30g and the borax of 30g, first Dissolve borax in 200g of water and heat to 90°C, stir for 5 minutes, then add nickel nitrate under stirring to make a plating solution;
[0024] b. Put the natural garnet matrix powder into the stirring pot, add the plating solution in step a, and stir for 10 minutes;
[0025] c. Put the natural garnet matrix powder mixed with the plating solution in step b into an oven, and dry at 160°C for 60 minutes;
[0026] d. Place the dried natural garnet matrix powder in step c in a kiln, raise the temperature to 80° C., keep it warm for 30 minutes, cool it down to normal temperature natura...
Embodiment 3
[0028] A kind of manufacture method of nickel-plated natural garnet wear-resistant material, it comprises the following steps:
[0029] a. Weigh 10kg of natural garnet matrix powder, the matrix powder is the standard particle size of No. 100, weigh 25g of nickel nitrate and 25g of borax, first dissolve borax in 250g of water and heat to 90°C, stir for 5 minutes , and then add nickel nitrate under stirring conditions to make a plating solution;
[0030] b. Put the natural garnet matrix powder into the stirring pot, add the plating solution in step a, and stir for 10 minutes;
[0031] c. Put the natural garnet matrix powder mixed with the plating solution in step b into an oven, and dry at 180°C for 60 minutes;
[0032] d. Place the dried natural garnet matrix powder in step c in a kiln, raise the temperature to 800° C., keep it warm for 30 minutes, cool it down to normal temperature naturally, and sieve the cooled matrix powder.
PUM
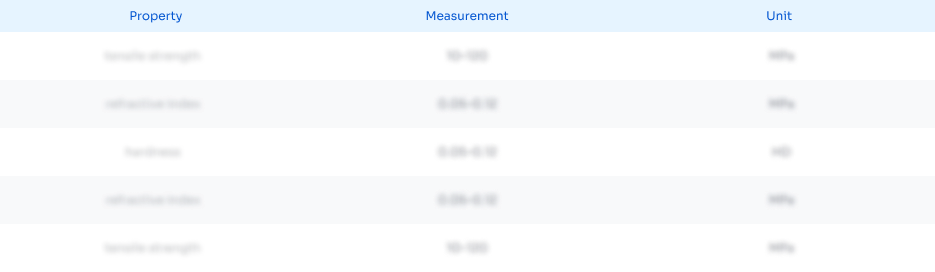
Abstract
Description
Claims
Application Information

- R&D
- Intellectual Property
- Life Sciences
- Materials
- Tech Scout
- Unparalleled Data Quality
- Higher Quality Content
- 60% Fewer Hallucinations
Browse by: Latest US Patents, China's latest patents, Technical Efficacy Thesaurus, Application Domain, Technology Topic, Popular Technical Reports.
© 2025 PatSnap. All rights reserved.Legal|Privacy policy|Modern Slavery Act Transparency Statement|Sitemap|About US| Contact US: help@patsnap.com