Natural fiber composite material and preparation method thereof
A natural fiber and composite material technology, applied in the field of natural fiber composite materials and its preparation, can solve the problems of high water absorption, cost increase, and perishability of natural fibers, and achieve the effect of simple operation steps
- Summary
- Abstract
- Description
- Claims
- Application Information
AI Technical Summary
Problems solved by technology
Method used
Examples
Embodiment 1
[0025] Take 30g of water-based epoxy resin, 100g of wood flour (natural fiber), 50g of silicone oil (filler), 3g of ethylenediamine (water-soluble hardener), 1g of tetrabutylammonium bromide (phase transfer catalyst) and water by weight ratio 200g.
[0026] 30g water-based epoxy resin is obtained by the following manner: take epoxy resin 15g, 4,4-azobis (4-cyanovaleric acid) (starter) 5g and styrene (monomer) 10g, epoxy resin The resin, 4,4-azobis(4-cyanovaleric acid) and styrene were put into a reaction kettle and mixed, and the mixture was obtained by reacting under pressure at 150° C. for 1 hour.
[0027] Add the above-mentioned water, water-based epoxy resin and ethylenediamine into the stirring tank, disperse the water-based epoxy resin and ethylenediamine in water to form an emulsion, then add tetrabutylammonium bromide, wood powder and silicone oil to mix evenly, at 80 The reaction was carried out at °C for 60 hours; after the reaction was completed, the reactant was t...
Embodiment 2
[0032] 70g of water-based epoxy resin, 500g of wood flour (natural fiber), 200g of lard (filler), 0.3g of ethylenediamine (water-soluble hardener), 0.01g of tetrabutylammonium bromide (phase transfer catalyst) by weight ratio g and water 100g.
[0033] 70g water-based epoxy resin is obtained by the following manner: take epoxy resin 49g, 4,4-azobis(4-cyanovaleric acid) (starter) 20g and styrene (monomer) 1g, epoxy resin The resin, 4,4-azobis(4-cyanovaleric acid) and styrene were put into a reaction kettle and mixed, and the mixture was obtained by reacting under pressure at 150° C. for 1 hour.
[0034] Add the above-mentioned water, water-based epoxy resin and ethylenediamine into the stirring tank, disperse the water-based epoxy resin and ethylenediamine in water to form an emulsion, then add tetrabutylammonium bromide, wood flour and lard to mix evenly, The reaction was carried out at 100° C. for 48 hours; after the reaction was completed, the reactant was transferred to an o...
Embodiment 3
[0039] Take 130g of water-based epoxy resin, 250g of wood powder (natural fiber), 500g of soil powder (filler), 5g of ethylenediamine (water-soluble hardener), 5g of tetrabutylammonium bromide (phase transfer catalyst) and Water 150g.
[0040] 130g water-based epoxy resin is obtained by the following manner: take 100g of epoxy resin, 20g of 4,4-azobis(4-cyanovaleric acid) (starting agent) and 10g of styrene (monomer), and epoxy The resin, 4,4-azobis(4-cyanovaleric acid) and styrene were put into a reaction kettle and mixed, and the mixture was obtained by reacting under pressure at 150° C. for 1 hour.
[0041] Add the above-mentioned water, water-based epoxy resin and ethylenediamine into the stirring tank, disperse the water-based epoxy resin and ethylenediamine in water to form an emulsion, then add tetrabutylammonium bromide, wood powder and soil powder to mix evenly, The reaction was carried out at 100° C. for 36 hours; after the reaction was completed, the reactant was t...
PUM
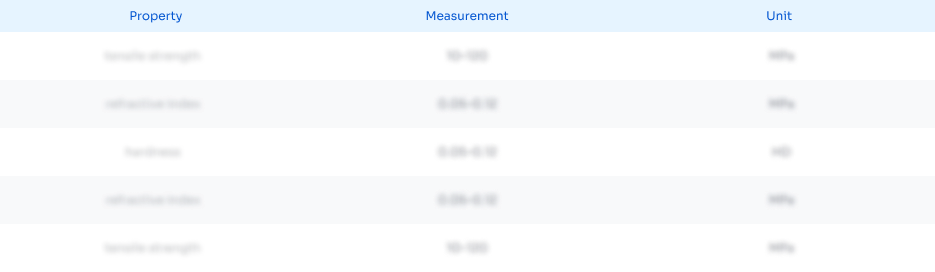
Abstract
Description
Claims
Application Information

- R&D
- Intellectual Property
- Life Sciences
- Materials
- Tech Scout
- Unparalleled Data Quality
- Higher Quality Content
- 60% Fewer Hallucinations
Browse by: Latest US Patents, China's latest patents, Technical Efficacy Thesaurus, Application Domain, Technology Topic, Popular Technical Reports.
© 2025 PatSnap. All rights reserved.Legal|Privacy policy|Modern Slavery Act Transparency Statement|Sitemap|About US| Contact US: help@patsnap.com