Environment-friendly flame retardant rubber material and preparation method thereof
A flame-retardant rubber, green and environmentally friendly technology, applied in the direction of fibrous fillers, dyed low-molecular organic compounds, etc., can solve the problems that the physical and mechanical properties of polymers are greatly affected, affect the performance of materials, human body, and environmental hazards, etc., to achieve Easy to implement, low production cost, good flame retardant effect
- Summary
- Abstract
- Description
- Claims
- Application Information
AI Technical Summary
Problems solved by technology
Method used
Examples
Embodiment 1
[0035] Soak 1 gram of sodium montmorillonite and 0.5 gram of dihydroxyethyltrimethyldodecyl ammonium bromide in 10 grams of 25% ethanol aqueous solution, stir for 20 minutes, heat to about 70°C, take out and dry to Constant weight; the product was filtered and washed with AgNO 3 (0.1 mol / L) test until there is no more white precipitate. Finally, vacuum-dry it at 100° C. for 4 hours and take it out to obtain organic montmorillonite.
[0036] 3# smoked sheet rubber: 100 parts; sulfur: 2 parts; accelerator M: 1 part; accelerator D: 0.2 parts; accelerator TMTD: 0.2 parts; stearic acid: 0.5 parts; zinc oxide: 3 parts; anti-aging Agent A: 1 part; organic montmorillonite: 5 parts; triaryl phosphate: 5 parts; placed in an open mill, and kneaded at 40° C. for 0.8 hours to obtain the flame-retardant rubber of the present invention.
[0037] The tensile properties, wear properties and flame retardant properties of the rubber are shown in Table 1.
Embodiment 2
[0039] Soak 1 gram of sodium montmorillonite and 0.8 gram of tetrabutylphosphine bromide in 20 grams of 40% ethanol aqueous solution, stir vigorously for 25 minutes, heat to about 65°C, take out and dry to constant weight; the product is filtered by suction and cleaning, followed by AgNO 3 (0.1 mol / L) test until there is no more white precipitate. Finally, vacuum-dry it at 110° C. for 3 hours, take it out, and obtain organic montmorillonite.
[0040] 3# smoked sheet rubber: 100 parts; sulfur: 2.5 parts; accelerator M: 1.3 parts; accelerator D: 0.3 parts; accelerator TMTD: 0.5 parts; stearic acid: 1 part; zinc oxide: 4 parts; anti-aging Agent A: 1.5 parts; organic montmorillonite: 5 parts; triaryl phosphate: 10 parts; placed in an open mill and kneaded at a temperature of 50° C. for 0.6 hours to obtain the flame-retardant rubber of the present invention.
[0041] The tensile properties, wear properties and flame retardant properties of the rubber are shown in Table 1.
Embodiment 3
[0043] Soak 1 gram of Na-montmorillonite and 1 gram of 1-ethyl-3-methylimidazolium tetrafluoroborate in 30 grams of 50% ethanol aqueous solution, stir vigorously for 30 minutes, and heat to about 60°C Take out and dry to constant weight; the product is filtered and washed with AgNO 3 (0.1 mol / L) test until there is no more white precipitate. Finally, vacuum-dry it at 120° C. for 2 hours and take it out to obtain organic montmorillonite.
[0044] 3# smoked sheet rubber: 100 parts; sulfur: 3 parts; accelerator M: 1.5 parts; accelerator D: 0.4 parts; accelerator TMTD: 0.8 parts; stearic acid: 1.5 parts; zinc oxide: 5 parts; anti-aging Agent A: 2 parts; organic montmorillonite: 10 parts; triaryl phosphate: 10 parts; placed in an open mill, and kneaded at a temperature of 60°C for 0.5 hours to obtain the flame-retardant rubber of the present invention.
[0045] The tensile properties, wear properties and flame retardant properties of the rubber are shown in Table 1.
[0046] ...
PUM
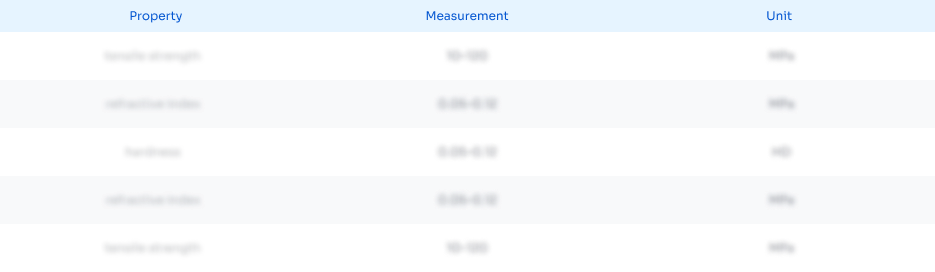
Abstract
Description
Claims
Application Information

- R&D
- Intellectual Property
- Life Sciences
- Materials
- Tech Scout
- Unparalleled Data Quality
- Higher Quality Content
- 60% Fewer Hallucinations
Browse by: Latest US Patents, China's latest patents, Technical Efficacy Thesaurus, Application Domain, Technology Topic, Popular Technical Reports.
© 2025 PatSnap. All rights reserved.Legal|Privacy policy|Modern Slavery Act Transparency Statement|Sitemap|About US| Contact US: help@patsnap.com