Method for controlling generation of cold crack in welding process based on electromagnetic induction heating
An electromagnetic induction heating and welding process technology, which is applied to welding equipment, auxiliary welding equipment, welding/cutting auxiliary equipment, etc., can solve the problems of increasing welding production process, changing the surface state of weld seam, and difficult control of flame power, etc., to achieve improved The effect of welding production efficiency, reduction of hardened structure and reduction of welding production process
- Summary
- Abstract
- Description
- Claims
- Application Information
AI Technical Summary
Problems solved by technology
Method used
Image
Examples
specific Embodiment approach 1
[0012] Specific implementation mode one: combine Figure 1-Figure 5 Describe this embodiment, the method of this embodiment is realized by the following steps:
[0013] Step 1: Find the welding continuous cooling transformation curve corresponding to the selected welding material; determine the austenite transformation temperature Ac 1 , martensite transformation temperature Ms, the longest time to form 100% martensite t 1 and the minimum time to form 0% martensite t 2 ;
[0014] Step 2: Determine the temperature field of the welding part of the workpiece to be welded; select a workpiece among the workpieces to be welded as the test piece, perform welding on the test piece, the welding process is consistent with the normal welding, and determine the quasi-stable temperature field of the test piece Ac 1 The distance between the points is L 1 , the distance between the arc center on the center line of the weld and the point at the martensitic transformation temperature Ms b...
specific Embodiment approach 2
[0019] Specific implementation mode two: combination figure 2 Describe the present embodiment, the characteristic dimension of the induction heating coil 7 of the present embodiment is length, width and longitudinal tube spacing, and the length is L=V in the step 3 1 ·t 2 , the width is to cover the weld seam and the heat-affected zone, and the longitudinal tube spacing is 19-21mm. Other components and connections are the same as those in the first embodiment.
specific Embodiment approach 3
[0020] Specific implementation mode three: combination figure 2 The present embodiment will be described. The induction heating coil 7 of the present embodiment is made of copper material. Other compositions and connections are the same as those in the first or second embodiment.
PUM
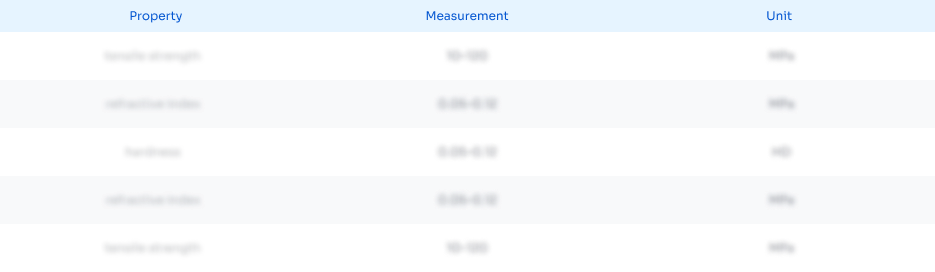
Abstract
Description
Claims
Application Information

- R&D
- Intellectual Property
- Life Sciences
- Materials
- Tech Scout
- Unparalleled Data Quality
- Higher Quality Content
- 60% Fewer Hallucinations
Browse by: Latest US Patents, China's latest patents, Technical Efficacy Thesaurus, Application Domain, Technology Topic, Popular Technical Reports.
© 2025 PatSnap. All rights reserved.Legal|Privacy policy|Modern Slavery Act Transparency Statement|Sitemap|About US| Contact US: help@patsnap.com