Method for preparing polyolefin microporous membrane through wet process
A polyolefin microporous membrane and polyolefin technology, applied in the polymer field, can solve the problems of poor pore uniformity of the microporous membrane, poor mechanical properties of the microporous membrane, residual solvent and detergent, etc. Low residue, high strength effect
- Summary
- Abstract
- Description
- Claims
- Application Information
AI Technical Summary
Problems solved by technology
Method used
Image
Examples
Embodiment 1
[0029] a At 250°C, the weight-average molecular weight of 20% of the total polyolefin will be 3.5×10 6 The ultra-high molecular weight polyethylene resin (125Kg) adds in the kneader and kneads, then it is cooled to 180 ℃, adds the weight-average molecular weight that accounts for 80% of polyolefin total amount again and is 3.5 * 10 5 High-density polyethylene (500Kg) and the nucleating agent zinc stearate (ZnSt 2 ) (5Kg), prepare polyolefin mixture;
[0030] b Add the obtained polyolefin mixture and liquid paraffin into a twin-screw extruder at a ratio of 1:4, extrude through a T-shaped die at 215°C, and cool the cooling roll to form a gel sheet, the temperature of the cooling roll is 35°C ;
[0031] c. Simultaneously biaxially stretch the obtained gel-like sheet 5×5 times at 115° C.;
[0032] d Immerse the stretched film in a dichloromethane solution at room temperature and normal pressure, and use ultrasonic extraction, the ultrasonic frequency is 20kHz, and the intensity...
Embodiment 2
[0035] a At 250°C, the weight-average molecular weight of 20% of the total polyolefin will be 3.5×10 6 The ultra-high molecular weight polyethylene resin (125Kg) adds in the kneader and kneads, then it is cooled to 180 ℃, adds the weight-average molecular weight that accounts for 80% of polyolefin total amount again and is 3.5 * 10 5 high-density polyethylene (500Kg) and the nucleating agent zinc stearate (ZnSt 2 ) (7.5Kg), preparing polyolefin mixture;
[0036] b Add the obtained polyolefin mixture and liquid paraffin (2000Kg) into the twin-screw extruder at a ratio of 1:4, extrude through a T-shaped die at 215°C, and cool the cooling roll to form a gel sheet. 35°C;
[0037] c. Simultaneously biaxially stretch the obtained gel-like sheet 5×5 times at 115° C.;
[0038] d Immerse the stretched film in a dichloromethane solution at room temperature and normal pressure, and use ultrasonic extraction, the ultrasonic frequency is 20kHz, and the intensity is 1.5W / cm 2 , the wash...
Embodiment 3
[0041] a At 250°C, the weight-average molecular weight of 20% of the total polyolefin will be 3.5×10 6 The ultra-high molecular weight polyethylene resin (125Kg) adds in the kneader and kneads, then it is cooled to 180 ℃, adds the weight-average molecular weight that accounts for 80% of polyolefin total amount again and is 3.5 * 10 5 High-density polyethylene (500Kg) and the nucleating agent zinc stearate (ZnSt 2 ) (5Kg), prepare polyolefin mixture;
[0042] b Add the obtained polyolefin mixture and liquid paraffin (2000Kg) into the twin-screw extruder at a ratio of 1:4, extrude through a T-shaped die at 215°C, and cool the cooling roll to form a gel sheet. 35°C;
[0043] c. Simultaneously biaxially stretch the obtained gel-like sheet 5×5 times at 115° C.;
[0044] d Immerse the stretched film in a dichloromethane solution at room temperature and normal pressure, and use ultrasonic extraction, the ultrasonic frequency is 50kHz, and the intensity is 1.5W / cm 2 , the washing ti...
PUM
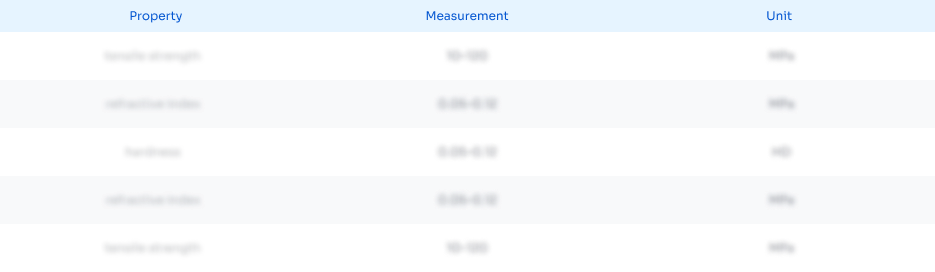
Abstract
Description
Claims
Application Information

- R&D
- Intellectual Property
- Life Sciences
- Materials
- Tech Scout
- Unparalleled Data Quality
- Higher Quality Content
- 60% Fewer Hallucinations
Browse by: Latest US Patents, China's latest patents, Technical Efficacy Thesaurus, Application Domain, Technology Topic, Popular Technical Reports.
© 2025 PatSnap. All rights reserved.Legal|Privacy policy|Modern Slavery Act Transparency Statement|Sitemap|About US| Contact US: help@patsnap.com