Micropore ceramic filter element and preparation method thereof
A technology of microporous ceramics and filter cores, applied in the field of ceramic filter cores, can solve the problems of high production cost of finished products, cumbersome production process, large production investment, etc., and achieve the effects of low production cost, low production cost and high production efficiency.
- Summary
- Abstract
- Description
- Claims
- Application Information
AI Technical Summary
Problems solved by technology
Method used
Examples
Embodiment 1
[0025] Diatomaceous earth (greater than 60 mesh) 30 Kaolin 10 Silica sol (30% silica content) 35
[0026] 10% content polyvinyl alcohol aqueous solution 24 ammonium bicarbonate 1
[0027] Its preparation method is as follows:
[0028] Weigh each raw material according to the percentage of formula quantity, and the operation steps are as follows:
[0029] ① Weigh each raw material according to the percentage of formula quantity.
[0030] ②Mix the binder and plasticizer evenly.
[0031] ③ Add the curing agent to the raw materials that have been mixed in step ② and mix well.
[0032] ④ Immediately add the raw materials mixed in step ③ to the filtered raw materials and mix well.
[0033] ⑤ Put the raw materials mixed in step ④ into the pre-prepared mold for extrusion or stamping to form an embryo, and then dry the moisture in the embryo body at a certain temperature to shape it, that is, to become porous micropores with a specified shape Ceramic filter.
Embodiment 2
[0035] Diatomaceous earth (greater than 100 mesh) 25 Kaolin 20 Silica sol (40% silica content) 40
[0036] 10% content polyvinyl alcohol aqueous solution 14 ammonium bicarbonate 1
[0037] Its preparation method is as follows:
[0038] Weigh each raw material according to the percentage of formula quantity, and the operation steps are as follows:
[0039] ① Weigh each raw material according to the percentage of formula quantity.
[0040] ②Mix the binder and plasticizer evenly.
[0041] ③ Add the curing agent to the raw materials that have been mixed in step ② and mix well.
[0042] ④ Immediately add the raw materials mixed in step ③ to the filtered raw materials and mix well.
[0043] ⑤Put the raw materials mixed in step ④ into the pre-prepared mold for extrusion or stamping to form an embryo, and then dry the moisture in the molded body at a certain temperature to shape it, that is, to become porous micropores with a specified shape Ceramic filter.
Embodiment 3
[0045] Diatomaceous earth (greater than 100 mesh) 35 Kaolin 10 Silica sol (40% silica content) 40
[0046] 2% content sodium carboxymethyl cellulose aqueous solution 12 sodium bicarbonate 3
[0047] Its preparation method is as follows:
[0048] Weigh each raw material according to the percentage of formula quantity, and the operation steps are as follows:
[0049] ① Weigh each raw material according to the percentage of formula quantity.
[0050] ②Mix the binder and plasticizer evenly.
[0051] ③ Add the curing agent to the raw materials that have been mixed in step ② and mix well.
[0052] ④ Immediately add the raw materials mixed in step ③ to the filtered raw materials and mix well.
[0053] ⑤Put the raw materials mixed in step ④ into the pre-prepared mold for extrusion or stamping to form an embryo, and then dry the moisture in the molded body at a certain temperature to shape it, that is, to become porous micropores with a specified shape Ceramic filter.
PUM
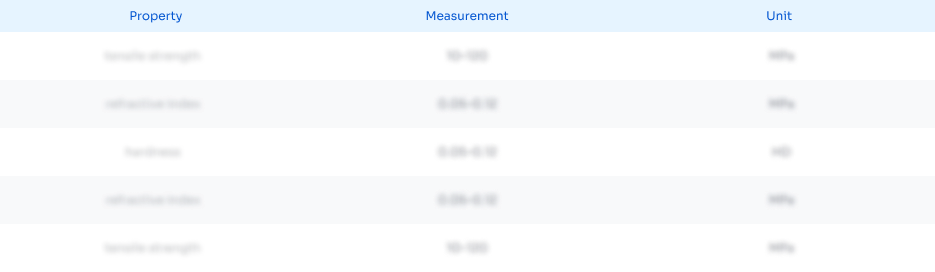
Abstract
Description
Claims
Application Information

- R&D
- Intellectual Property
- Life Sciences
- Materials
- Tech Scout
- Unparalleled Data Quality
- Higher Quality Content
- 60% Fewer Hallucinations
Browse by: Latest US Patents, China's latest patents, Technical Efficacy Thesaurus, Application Domain, Technology Topic, Popular Technical Reports.
© 2025 PatSnap. All rights reserved.Legal|Privacy policy|Modern Slavery Act Transparency Statement|Sitemap|About US| Contact US: help@patsnap.com