Production method of active carbon of direct carbon conversion fuel cell
A fuel cell and activated carbon technology, applied in battery electrodes, circuits, electrical components, etc., can solve the problems of high ash content, poor electrical conductivity, and low reactivity, and achieve low ash content, good electrical conductivity, and favorable electrical conductivity Effect
- Summary
- Abstract
- Description
- Claims
- Application Information
AI Technical Summary
Problems solved by technology
Method used
Examples
Embodiment 1
[0017] (1) KOH and K 2 CO 3 Prepare composite activator according to 1:1, then weigh composite activator and oak carbonization material according to mass ratio 4:1, add distilled water and mix evenly, impregnate at room temperature for 12h, then at 120°C temperature, under 150ml / min nitrogen dry. The dried mixture was placed in a reactor under a nitrogen flow for activation. The activation temperature was 800° C. and the activation time was 60 min. After the activation was completed, it was cooled to room temperature. Finally, the activated carbon was repeatedly washed and filtered with distilled water until the filtrate was neutral, dried under nitrogen protection at 120°C, collected and set aside.
[0018] (2) According to 2% loading Ni relative to the weight of activated carbon, add distilled water to the mixture and stir evenly, and dry under the protection of nitrogen. The dried raw materials were put into the reactor, heated to 900°C at a heating rate of 5°C / min and a...
Embodiment 2
[0022] (1) KOH and K 2 CO 3 Prepare composite activator according to 1:1, then weigh composite activator and oak carbonized material according to the mass ratio of 3:1, add distilled water and mix evenly, impregnate at room temperature for 12h, and then at a temperature of 120°C, under nitrogen gas of 150ml / min dry. The dried mixture was placed in a reactor under a nitrogen flow for activation. The activation temperature was 800° C. and the activation time was 60 min. After the activation was completed, it was cooled to room temperature. Finally, the activated carbon was repeatedly washed and filtered with distilled water until the filtrate was neutral, dried under nitrogen protection at 120°C, collected and set aside.
[0023] (2) According to 2% loading Ni relative to the weight of activated carbon, add distilled water to the mixture and stir evenly, and dry under the protection of nitrogen. The dried raw materials were put into the reactor, heated to 900°C at a heating r...
Embodiment 3
[0027] (1) Weigh K according to the mass ratio of 1:1 2 CO 3 Add distilled water and mix well with oak charcoal material, impregnate at room temperature for 12h, and then dry at 120°C and 150ml / min nitrogen. The dried mixture was placed in a reactor under a nitrogen flow for activation. The activation temperature was 900° C. and the activation time was 120 min. After the activation was completed, it was cooled to room temperature. Finally, the activated carbon was repeatedly washed and filtered with distilled water until the filtrate was neutral, dried under nitrogen protection at 120°C, collected and set aside.
[0028] (2) According to 5% loading Ni relative to the weight of activated carbon, add distilled water to the mixture and stir evenly, and dry under the protection of nitrogen. The dried raw materials were put into the reactor, heated to 900°C at a heating rate of 5°C / min and a nitrogen flow rate of 100ml / min, kept for 120min, and then cooled naturally.
[0029] (3...
PUM
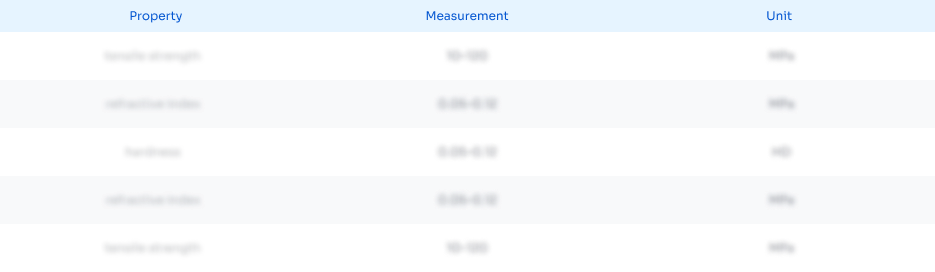
Abstract
Description
Claims
Application Information

- R&D
- Intellectual Property
- Life Sciences
- Materials
- Tech Scout
- Unparalleled Data Quality
- Higher Quality Content
- 60% Fewer Hallucinations
Browse by: Latest US Patents, China's latest patents, Technical Efficacy Thesaurus, Application Domain, Technology Topic, Popular Technical Reports.
© 2025 PatSnap. All rights reserved.Legal|Privacy policy|Modern Slavery Act Transparency Statement|Sitemap|About US| Contact US: help@patsnap.com