Metal tube flaring molding machine
A forming machine and metal tube technology, applied in the field of metal tube flaring forming machines, can solve problems such as low production efficiency, high energy consumption, and welding residues of pipe fittings, and achieve high production efficiency, low noise, and less pollution.
- Summary
- Abstract
- Description
- Claims
- Application Information
AI Technical Summary
Problems solved by technology
Method used
Image
Examples
Embodiment Construction
[0016] The present invention will be further described in detail below in conjunction with the accompanying drawings and embodiments.
[0017] In the embodiment shown in the figure, the reference numerals explain: punch 1, clamping die assembly 2, inclined block 21, first inclined surface 21a, clamping member 22, second inclined surface 22a, gas-hydraulic booster cylinder 3, clamping Cylinder 4, compression cylinder 5, push plate 6, fixed plate 7, slide block groove 7a, slide block 8, slide block cylinder 9, baffle plate 10.
[0018] As shown in the figure, a metal tube flaring forming machine includes a frame, a punch 1 arranged on the frame, and two clamping die assemblies 2 that cooperate with the punch 1 The clamping die, the rear end of the punch 1 is connected with a gas-liquid booster cylinder 3, and the two clamping die components 2 are connected with a clamping cylinder 4.
[0019] Wherein, the clamping mold assembly 2 of the clamping cylinder 4 includes an inclined ...
PUM
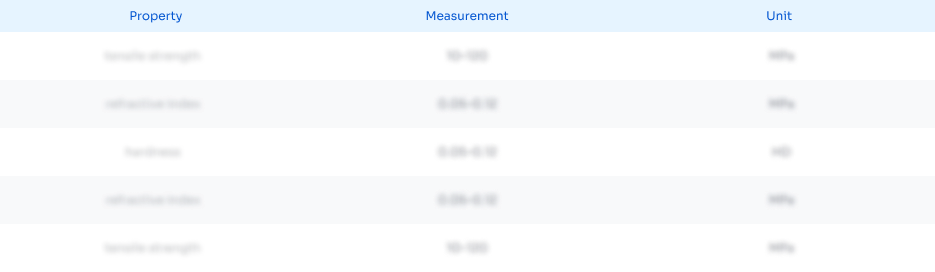
Abstract
Description
Claims
Application Information

- R&D Engineer
- R&D Manager
- IP Professional
- Industry Leading Data Capabilities
- Powerful AI technology
- Patent DNA Extraction
Browse by: Latest US Patents, China's latest patents, Technical Efficacy Thesaurus, Application Domain, Technology Topic, Popular Technical Reports.
© 2024 PatSnap. All rights reserved.Legal|Privacy policy|Modern Slavery Act Transparency Statement|Sitemap|About US| Contact US: help@patsnap.com