Sintering-free flyash brick
A fly ash brick, sinter-free technology, applied in the field of building materials, can solve the problems of low heat energy utilization rate, high vegetation cost, cumbersome adjustment, etc., and achieve the effects of environmental protection, strong frost resistance, and simple manufacturing process
- Summary
- Abstract
- Description
- Claims
- Application Information
AI Technical Summary
Problems solved by technology
Method used
Examples
Embodiment 1
[0019] The formula is:
[0020] 60 parts of fly ash, 18 parts of slag, 15 parts of calcium carbide slag, 2 parts of citric acid slag, 6 parts of yellow sand, 0.1 part of sodium nitrite, 0.2 part of sodium sulfate, 0.5 part of sodium silicate, 0.01 part of triethanolamine, rare earth dust 0.5 parts, water 8 parts, water glass 0.03 parts, salt 0.15 parts.
[0021] Its preparation method consists of the following steps:
[0022] (1) Stir after mixing 60 parts of fly ash and 15 parts of carbide slag according to the formula;
[0023] (2) The mixture obtained in step (1) is sent into a high-speed finely crushed pair of rollers, broken and wheel milled;
[0024] (3) Mix the crushed and wheel-milled mixture with 18 parts of slag, 2 parts of citric acid slag, 6 parts of yellow sand, 0.1 part of sodium nitrite, 0.2 part of sodium sulfate, 0.5 part of sodium silicate, and 0.01 part of triethanolamine according to the formula , 0.5 parts of rare earth dust, 8 parts of water, 0.03 part...
Embodiment 2
[0028] The formula is:
[0029] 65 parts of fly ash, 14 parts of slag, 12 parts of calcium carbide slag, 1.5 parts of citric acid slag, 4.5 parts of yellow sand, 0.15 parts of sodium nitrite, 0.35 parts of sodium sulfate, 0.75 parts of sodium silicate, 0.015 parts of triethanolamine, rare earth dust 0.3 parts, water 15 parts, water glass 0.02 parts, salt 0.3 parts.
[0030] Its preparation method consists of the following steps:
[0031] (1) Stir after mixing 65 parts of fly ash and 12 parts of carbide slag according to the formula;
[0032] (2) The mixture obtained in step (1) is sent into a high-speed finely crushed pair of rollers, broken and wheel milled;
[0033] (3) Mix the crushed and wheel-milled mixture with 14 parts of slag, 1.5 parts of citric acid slag, 4.5 parts of yellow sand, 0.15 part of sodium nitrite, 0.35 part of sodium sulfate, 0.75 part of sodium silicate, and 0.015 part of triethanolamine according to the formula , 0.3 parts of rare earth dust, 15 part...
Embodiment 3
[0037] The formula is:
[0038] 70 parts of fly ash, 10 parts of slag, 10 parts of calcium carbide slag, 1 part of citric acid slag, 3 parts of yellow sand, 0.2 part of sodium nitrite, 0.5 part of sodium sulfate, 1 part of sodium silicate, 0.02 part of triethanolamine, rare earth dust 0.1 part, 0.01 part of water glass, 22.5 parts of water, 0.4 part of table salt.
[0039] Its preparation method consists of the following steps:
[0040] (1) Stir after mixing 70 parts of fly ash and 10 parts of carbide slag according to the formula;
[0041] (2) The mixture obtained in step (1) is sent into a high-speed finely crushed pair of rollers, broken and wheel milled;
[0042] (3) Mix the crushed and wheel-milled mixture with 10 parts of slag, 1 part of citric acid slag, 3 parts of yellow sand, 0.2 part of sodium nitrite, 0.5 part of sodium sulfate, 1 part of sodium silicate, and 0.02 part of triethanolamine according to the formula , 0.1 part of rare earth dust, 0.03 part of water g...
PUM
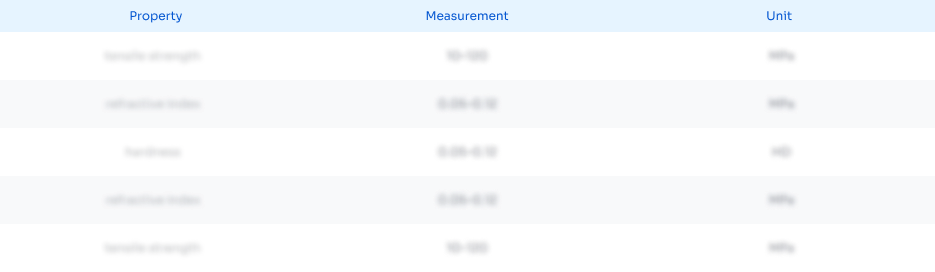
Abstract
Description
Claims
Application Information

- R&D Engineer
- R&D Manager
- IP Professional
- Industry Leading Data Capabilities
- Powerful AI technology
- Patent DNA Extraction
Browse by: Latest US Patents, China's latest patents, Technical Efficacy Thesaurus, Application Domain, Technology Topic, Popular Technical Reports.
© 2024 PatSnap. All rights reserved.Legal|Privacy policy|Modern Slavery Act Transparency Statement|Sitemap|About US| Contact US: help@patsnap.com