Preparation method of composite MnO2 anode material for chargeable Li-Mn battery
A positive electrode material, lithium-manganese battery technology, applied in the direction of battery electrodes, circuits, electrical components, etc., can solve the problems of rare rechargeable composite MnO2 research, rare battery industrial development, etc., to improve the charging and discharging effect, 3V platform Stable, homogeneous effect
- Summary
- Abstract
- Description
- Claims
- Application Information
AI Technical Summary
Problems solved by technology
Method used
Examples
Embodiment 1
[0020] Commercially available electrolytic MnO with γ-crystal form and an average grain diameter of 30 μm 2 Soak in 1M sulfuric acid aqueous solution at 40°C for 10 hours, sulfuric acid solution and MnO 2 The weight ratio is 1:5. Then the suspension was filtered through a plastic plate and frame filter press to filter out MnO 2 Solid, washed 3 times with water until the solution does not contain sulfate ions. The weight ratio of water and wet materials during washing is 1:3. The washed material is made into a suspension again according to the weight ratio of water and wet material at 1:3, and is ground by a high-speed rotating colloid mill.
[0021] The MnO after the above steps 2 Add AEO (fatty alcohol polyoxyethylene ether) with a weight ratio of 0.3% to the / water slurry, stir evenly, put it into a sealed reaction kettle, heat the material to 120° C., and keep the temperature constant for 3 hours in the stirring state. Cool down to below 70°C, filter through plastic pl...
Embodiment 2
[0023] Commercially available electrolytic MnO with γ crystal form and an average grain diameter of 50 μm 2 Soak in 3M sulfuric acid aqueous solution at 50°C for 15 hours, the weight ratio of sulfuric acid solution and manganese dioxide is 1:5. Then the suspension was filtered through a plastic plate and frame filter press to filter out MnO 2Solid, washed 5 times with water until the solution does not contain sulfate ions. The weight ratio of water and wet materials during washing is 1:3. The washed material is made into a suspension again according to the weight ratio of water and wet material at 1:3, and is ground by a high-speed rotating colloid mill.
[0024] The MnO after the above steps 2 Add Tween (polyoxyethylene sorbitan fatty acid ester) with a weight ratio of 0.5% to the / water slurry, stir evenly, put into a sealed reaction kettle, heat the material to 140° C., and keep the temperature constant for 5 hours in the stirring state. Cool down to below 70°C, filter ...
Embodiment 3
[0026] Commercially available electrolytic MnO with γ crystal form and an average grain diameter of 40 μm 2 Soak in 2M sulfuric acid aqueous solution at 45°C for 12 hours, sulfuric acid solution and MnO 2 The weight ratio is 1:5. Then the suspension was filtered through a plastic plate and frame filter press to filter out MnO 2 Solid, washed 4 times with water until the solution does not contain sulfate ions. The weight ratio of water and wet materials during washing is 1:3. The washed material is made into a suspension again according to the weight ratio of water and wet material at 1:3, and is ground by a high-speed rotating colloid mill.
[0027] The MnO after the above steps 2 Add OP (alkylphenol polyoxyethylene ether) with a weight ratio of 0.4% to the / water slurry, stir evenly, put it into a sealed reaction kettle, heat the material to 130° C., and keep the temperature constant for 4 hours in the stirring state. Cool down to below 70°C, filter through plastic plate...
PUM
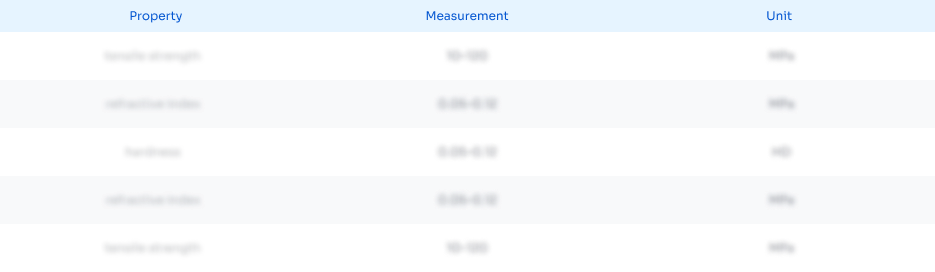
Abstract
Description
Claims
Application Information

- R&D Engineer
- R&D Manager
- IP Professional
- Industry Leading Data Capabilities
- Powerful AI technology
- Patent DNA Extraction
Browse by: Latest US Patents, China's latest patents, Technical Efficacy Thesaurus, Application Domain, Technology Topic, Popular Technical Reports.
© 2024 PatSnap. All rights reserved.Legal|Privacy policy|Modern Slavery Act Transparency Statement|Sitemap|About US| Contact US: help@patsnap.com