Multi-axis capacitive accelerometer
An accelerometer, capacitive technology, applied in the design field of multi-axis capacitive accelerometer, can solve the problem of reducing the effective area utilization rate and so on
- Summary
- Abstract
- Description
- Claims
- Application Information
AI Technical Summary
Problems solved by technology
Method used
Image
Examples
Embodiment Construction
[0105] Figure 4 It is a top view of a multi-axis capacitive accelerometer according to an embodiment of the present invention. Figure 5 for Figure 4 Sectional view along line I-I. Please refer to Figure 4 and Figure 5 , the multi-axis capacitive accelerometer 1000 of this embodiment includes a substrate 1100 and a structural layer 1200 . A plurality of sensing electrodes 1120 are disposed on the surface 1110 of the substrate 1100 . The structural layer 1200 includes a plurality of fixed seats 1210, a first mass 1220, a first elastic structure 1230, a plurality of fixed sensing masses 1240, a second mass 1250, a third mass 1260, a second elastic structure 1270 and a third mass. Elastic structure 1280.
[0106] The first mass 1220 is disposed above the surface 1110 of the substrate 1100 , and the first mass 1220 has a central axis 1222 and a first opening 1224 and a second opening 1226 inside the first mass 1220 . The first opening 1224 and the second opening 1226 ar...
PUM
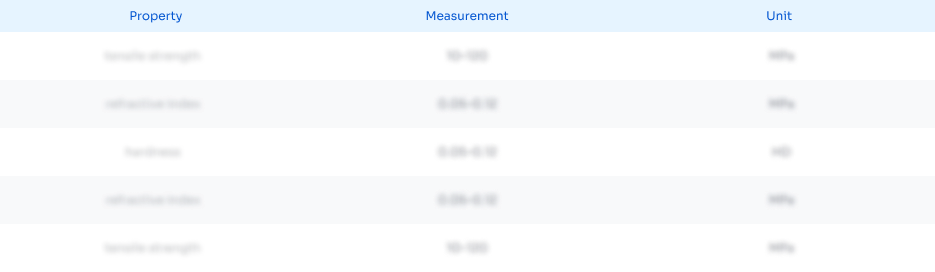
Abstract
Description
Claims
Application Information

- Generate Ideas
- Intellectual Property
- Life Sciences
- Materials
- Tech Scout
- Unparalleled Data Quality
- Higher Quality Content
- 60% Fewer Hallucinations
Browse by: Latest US Patents, China's latest patents, Technical Efficacy Thesaurus, Application Domain, Technology Topic, Popular Technical Reports.
© 2025 PatSnap. All rights reserved.Legal|Privacy policy|Modern Slavery Act Transparency Statement|Sitemap|About US| Contact US: help@patsnap.com