Manufacturing method of Modundai mink knitted velour
A manufacturing method, the technology of Morton Dai mink, applied in the field of textile industry, can solve the problems of easy shedding, expensive wool, poor fabric resilience, etc., achieve comfortable and warm wearing, and solve the problems of easy lint pilling and fabric rebound. good elasticity
- Summary
- Abstract
- Description
- Claims
- Application Information
AI Technical Summary
Problems solved by technology
Method used
Examples
Embodiment 1
[0011] Embodiment 1: a kind of manufacture method of Morton Dai mink knitted cashmere adopts the following process steps:
[0012] Processing of mink velvet single yarn: Wet the mink velvet loose fibers after washing and dyeing in layers, and add and hair oil, and the weight ratio of hair oil and water is 1:10, the moisture regain is 20%, store 24 hours; After layering and wetting, slitting is carried out on a quadruple carding machine to form mink velvet roving, the count of which is 20Nm; the mink velvet roving is stored at constant temperature and humidity for 24 hours, the temperature is 25°C, and the humidity is 75% RH; After storage at constant temperature and humidity, spinning on the mule spinning frame forms mink velvet single yarn, the spinning draft ratio is 1.2, the spinning count is 24Nm, the spinning twist is 350 twists / m, and the spinning is Z twist; the mink velvet single yarn is softened for the second time and is ready for use.
[0013] Processing of lamb ve...
Embodiment 2
[0015] Embodiment two: a kind of manufacture method of Morton Dai mink knitted cashmere, adopt following process steps:
[0016] The processing method of mink cashmere single yarn and lamb cashmere ply yarn is regarded as embodiment one.
[0017] The mink cashmere single yarn was subjected to constant temperature and humidity for 24 hours, the temperature was 25°C, and the relative humidity was 75%RH; the lamb cashmere yarn was subjected to constant temperature and humidity for 24 hours, the temperature was 25°C, and the relative humidity was 75%RH; The mink velvet single yarn and 1 lamb velvet ply yarn are combined and twisted on the twisting machine, the twist is 150 twists / m, S twist, and the spindle speed is 5500 revolutions / minute; then it is rewound through the winder to become package yarn; Wet the package yarn with a moisture regain rate of 16%; finally form a ball on the FB828 ball forming machine.
Embodiment 3
[0018] Embodiment three: the processing method of mink cashmere single yarn and lamb cashmere ply yarn is regarded as embodiment one.
[0019] A kind of manufacture method of Morton Dai mink knitted fleece adopts the following process steps:
[0020] The mink velvet single yarn was subjected to constant temperature and humidity for 24 hours, the temperature was 30°C, and the relative humidity was 80%RH; the lamb velvet yarn was subjected to constant temperature and humidity for 24 hours, the temperature was 30°C, and the relative humidity was 80%RH; The mink velvet single yarn and 1 lamb velvet ply yarn are merged and twisted on the twisting machine, the twist is 200 twists / m, S twist, and the spindle speed is 6000 revolutions / minute; then it is rewound through the winder to become package yarn; Wet the cheese with a moisture regain rate of 18%; finally form a ball on the FB828 ball forming machine.
PUM
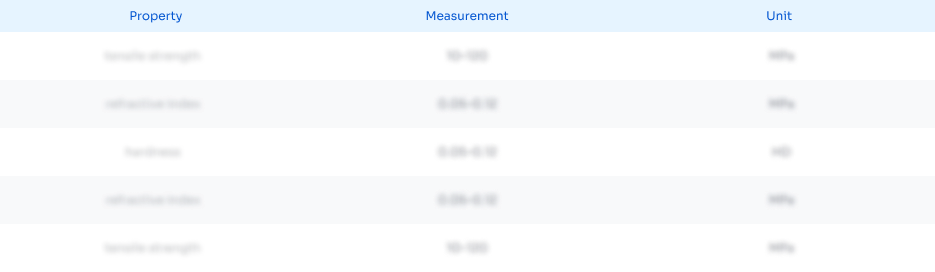
Abstract
Description
Claims
Application Information

- R&D Engineer
- R&D Manager
- IP Professional
- Industry Leading Data Capabilities
- Powerful AI technology
- Patent DNA Extraction
Browse by: Latest US Patents, China's latest patents, Technical Efficacy Thesaurus, Application Domain, Technology Topic, Popular Technical Reports.
© 2024 PatSnap. All rights reserved.Legal|Privacy policy|Modern Slavery Act Transparency Statement|Sitemap|About US| Contact US: help@patsnap.com