Brazed aluminum alloy foil with high strength and high corrosion resistance and manufacturing method thereof
A technology of aluminum alloy foil and manufacturing method, which is applied in the directions of metal rolling, temperature control, rolling force/roll gap control, etc., and can solve the problems of reduced corrosion performance and processing performance of alloys, and easy segregation.
- Summary
- Abstract
- Description
- Claims
- Application Information
AI Technical Summary
Problems solved by technology
Method used
Examples
Embodiment Construction
[0015] According to the alloy composition range designed by the present invention, adopt 99.7Al ingot and Mn, Si, Fe agent and Al10Zr, Al10Ti, Al5Cr and Al5V master alloy, mix a kind of alloy A-1 and 3003 alloys (see table 1) by weight ratio. In a 5TKg class flame furnace, after smelting and refining, it is semi-continuously cast into a flat ingot of 160mm×600mm×2100mm, the pouring temperature is 710-720°C; it is kept at 610°C for 12 hours for homogenization, and after milling, press 12 %thickness ratio Combined into a composite ingot, heated in a Kw resistance furnace at 550°C for 2 hours, hot rolled to a thickness of 7.5mm, cold rough rolled to 1.2mm, annealed at 430°C for 2 hours, cold finish rolled to 0.25mm, and then annealed at 430°C 2h cold finish rolling to finished product thickness 0.18mm.
[0016] Through the DSC melting point measurement of the above composition alloy and 3003 alloy 650×0.08mm foil, the tensile properties are in accordance with "Metal Tensile Test ...
PUM
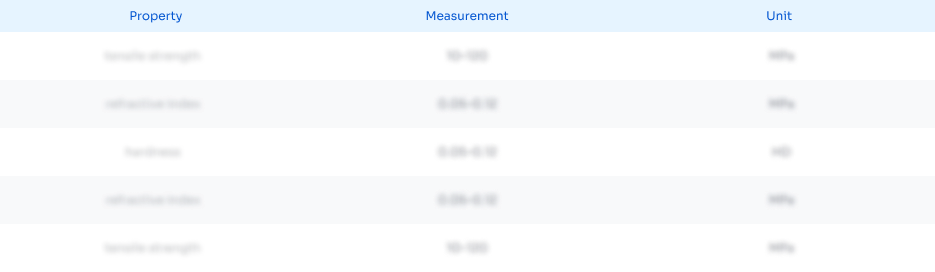
Abstract
Description
Claims
Application Information

- R&D Engineer
- R&D Manager
- IP Professional
- Industry Leading Data Capabilities
- Powerful AI technology
- Patent DNA Extraction
Browse by: Latest US Patents, China's latest patents, Technical Efficacy Thesaurus, Application Domain, Technology Topic, Popular Technical Reports.
© 2024 PatSnap. All rights reserved.Legal|Privacy policy|Modern Slavery Act Transparency Statement|Sitemap|About US| Contact US: help@patsnap.com