Bleaching production method for washing iron-dyed kaolin
A production method and kaolin technology, applied in aluminum silicate, silicate and other directions, can solve the problems of uneconomical economy, low iron removal efficiency, complex process, etc., and achieve controllable production process, considerable market prospects, and simple operation. Effect
- Summary
- Abstract
- Description
- Claims
- Application Information
AI Technical Summary
Problems solved by technology
Method used
Image
Examples
Embodiment 1
[0038] A subway in Fujian Province was used to dye kaolin. After washing, the natural whiteness of 325 mesh iron-dyed kaolin is 65%, the content of Fe in kaolin is 0.95%, and the content of Al is 37.8%. The main mineral composition is kaolinite and a very small amount of muscovite and quartz; Minerals mainly exist in irregular lamellar shape, with a small amount of tubular shape, and the whole is flocculent. Add the 325-mesh washed iron-dyed kaolin slurry with a converted dry weight of 20 tons into the bleaching tank, add water and stir to adjust the slurry concentration to 25%. Add concentrated sulfuric acid to adjust the pH value of the slurry to 3, add 3% sodium hydrosulfite to react for 45 minutes, and then add 0.8% oxalic acid to react for 15 minutes. Add water to wash 3 times until the pH value of the pulp is 6.5, drain the water after sedimentation, and the concentration of the precipitated product pulp reaches 32%. Put the bleached washing water into the wastewater t...
Embodiment 2
[0040] Adopted raw material and bleaching process are with embodiment 1. After conversion, the dry weight of kaolin is 15 tons, and the pulp concentration is 20%. The pH value of the pulp is 3, the amount of hydrosulfite added is 3%, the reaction time is 45min, the amount of oxalic acid is added 0.8%, the reaction time is 15min, and the pulp is washed 3 times until the pH value of the pulp is 7, and the concentration of the precipitated product pulp reaches 30%. Put the bleached washing water into the wastewater treatment tank, and add 0.8‰ quicklime while stirring to adjust the pH value of the wastewater to about 7. After stirring for 30 minutes, let it stand still for 5-6 hours, put clean water into the clean water pool, and waste residue treatment After multiple wastewater treatments, place the waste residue pool. Chemical analysis determined an iron content of 0.41% and an aluminum content of 37.13%, with no change in mineral composition and structure after bleaching. Th...
Embodiment 3
[0042] Adopted raw material and bleaching process are with embodiment 1. After conversion, the dry weight of kaolin is 30 tons, and the pulp concentration is 35%. The pH value of the pulp is 3, the amount of sodium hydrosulfite added is 3%, the reaction time is 45 minutes, the amount of oxalic acid is added 0.8%, the reaction time is 15 minutes, and the pH value of the pulp is 7 after washing for 3 times, and the concentration of the precipitated product pulp reaches 38%. Put the bleached washing water into the wastewater treatment tank, and add 0.8‰ quicklime while stirring to adjust the pH value of the wastewater to about 7. After stirring for 30 minutes, let it stand still for 5-6 hours, put clean water into the clean water pool, and waste residue treatment After multiple wastewater treatments, place the waste residue pool. Chemical analysis determined an iron content of 0.53% and an aluminum content of 36.99%, with no change in mineral composition and structure after blea...
PUM
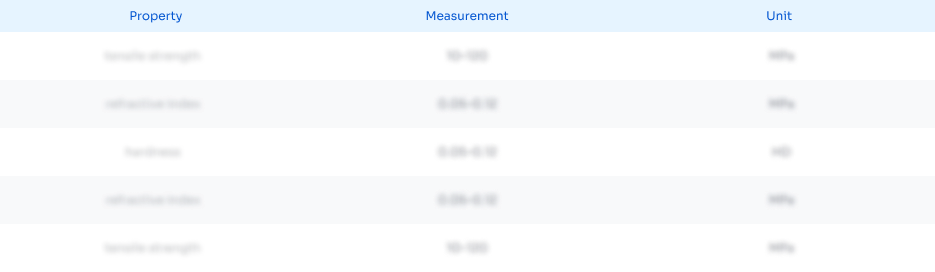
Abstract
Description
Claims
Application Information

- R&D
- Intellectual Property
- Life Sciences
- Materials
- Tech Scout
- Unparalleled Data Quality
- Higher Quality Content
- 60% Fewer Hallucinations
Browse by: Latest US Patents, China's latest patents, Technical Efficacy Thesaurus, Application Domain, Technology Topic, Popular Technical Reports.
© 2025 PatSnap. All rights reserved.Legal|Privacy policy|Modern Slavery Act Transparency Statement|Sitemap|About US| Contact US: help@patsnap.com