Injection molding zipper
A technology of zipper and chain elements, which is applied in the field of zippers, can solve the problem of insufficient bonding force between injection molded zipper elements and cloth tape, and achieve the effect of improving the bonding force
- Summary
- Abstract
- Description
- Claims
- Application Information
AI Technical Summary
Problems solved by technology
Method used
Image
Examples
Embodiment 1
[0021] Such as figure 1 As shown, the injection molded zipper of the present invention comprises: chain element 1, cloth tape 6, and described cloth tape 6 is made up of central line 5, a group of warp threads 3 and continuous weft thread 2; cloth tape 6 contacts with chain element 1 and is drawn The part covered by the fastener element 1 is the joint surface area of the tape 6, and the meridional continuous tape part of the joint surface is the core area 8 of the tape 6, and a row of edges is set beside the center line 5 in the core area 8. The small holes 4 evenly distributed in the direction of the warp 3, and the spacing of the small holes 4 ensure that there are at least one or more small holes 4 in the joint surface area between the cloth tape 6 and each individual fastener element 1 . The injection molding material liquid heated and melted by the injection molding machine in the production process of the injection molding zipper is extruded by the screw of the injecti...
Embodiment 2
[0024] Such as image 3 As shown, the central line 5 in the core region 8 of the cloth tape 6 in the injection molded zipper of the present invention is thinned, and the number of warps 3 in the core region 8 of the injection molded zipper cloth 6 is increased, and in the core region of the cloth tape 6 Two or more rows of evenly distributed small holes 4 are arranged in a staggered arrangement in the direction of the warp 3 in 8, and the spacing of the small holes 4 ensures that there are at least two or two The above small holes 4; in this way, there are at least two plastic columns 9 in the joint surface area of each element 1 of the injection molded zipper and the cloth tape 6 after production; the bonding force of the elements 1 of the injection molded zipper and the cloth tape 6 will be greater. promote. Other unmentioned specific structures of the injection molded zipper in this embodiment are the same as those in Embodiment 1 of the present invention.
Embodiment 3
[0026] Such as Figure 4 As shown, the cloth tape 6 in the injection molded zipper of the present invention is not provided with a center line 5, and a row or two or more rows of evenly distributed small Hole 4, the interval between small holes 4 ensures that there is at least one or more small holes 4 in the joint surface area between cloth tape 6 and each fastener element 1; in this way, each fastener element 1 of the injection molded zipper is combined with cloth tape 6 after production. There are at least one or more plastic material columns 9 in the surface area. Other unmentioned specific structures of the injection molded zipper in this embodiment are the same as those in Embodiment 1 of the present invention.
PUM
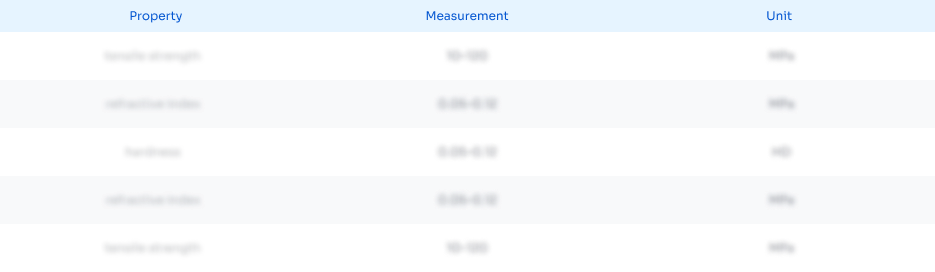
Abstract
Description
Claims
Application Information

- R&D Engineer
- R&D Manager
- IP Professional
- Industry Leading Data Capabilities
- Powerful AI technology
- Patent DNA Extraction
Browse by: Latest US Patents, China's latest patents, Technical Efficacy Thesaurus, Application Domain, Technology Topic, Popular Technical Reports.
© 2024 PatSnap. All rights reserved.Legal|Privacy policy|Modern Slavery Act Transparency Statement|Sitemap|About US| Contact US: help@patsnap.com