Method and device for efficiently producing polycrystalline silicon
A production method and technology for polycrystalline silicon, which are applied in the growth of polycrystalline materials, crystal growth, and single crystal growth, etc., can solve the problems of declining factory income, waste of raw materials, and reduced output, so as to reduce the difficulty of exhaust gas treatment and improve the one-time yield. , the effect of saving production costs
- Summary
- Abstract
- Description
- Claims
- Application Information
AI Technical Summary
Problems solved by technology
Method used
Image
Examples
Embodiment 1
[0034] The raw material mixture gas composed of trichlorosilane and hydrogen at a volume ratio of 1:10 first enters the tube heat exchanger for heating, then enters the plate heat exchanger for heat exchange, and then enters the polysilicon reduction reactor for reaction to maintain the raw material gas in the reduction process. The inlet temperature of the reactor is 300°C; in the tube heat exchanger, the raw material gas exchanges heat with the tail gas produced in the polysilicon production process, and in the plate heat exchanger, the raw material gas exchanges heat with water vapor;
[0035] In the polysilicon reduction reactor, the initial hydrogen flow rate is 100Nm 3 / h, under the conditions of 1080°C and 2Mpa, the raw material mixture gas reacts to deposit polysilicon on the surface of the silicon core. When the silicon core grows to a diameter of 50mm, stop applying the current and adjust the hydrogen flow rate to 200Nm 3 / h;
[0036] When the surface temperature of...
Embodiment 2
[0042] The raw material mixture composed of trichlorosilane and hydrogen at a volume ratio of 1:15 first enters the tube heat exchanger for heating, then enters the plate heat exchanger for heat exchange, and then enters the polysilicon reduction reactor for reaction to maintain the raw material gas in the reduction process. The inlet temperature of the reactor is 300°C; in the tube heat exchanger, the raw material gas exchanges heat with the tail gas produced in the polysilicon production process, and in the plate heat exchanger, the raw material gas exchanges heat with water vapor;
[0043] In the polysilicon reduction reactor, the initial hydrogen flow rate is 100Nm 3 / h, under the conditions of 1100°C and 2Mpa, the raw material mixture gas reacts to deposit polysilicon on the surface of the silicon core. When the silicon core grows to a diameter of 50mm, stop applying the current and adjust the hydrogen flow rate to 200Nm 3 / h;
[0044] When the surface temperature of the...
Embodiment 3
[0050] The raw material mixture gas composed of trichlorosilane and hydrogen at a volume ratio of 1:2 first enters the tube heat exchanger for heating, then enters the plate heat exchanger for heat exchange, and then enters the polysilicon reduction reactor for reaction to maintain the raw material gas in the reduction process. The inlet temperature of the reactor is 300°C; in the tube heat exchanger, the raw material gas exchanges heat with the tail gas produced in the polysilicon production process, and in the plate heat exchanger, the raw material gas exchanges heat with water vapor;
[0051] In the polysilicon reduction reactor, the initial hydrogen flow rate is 100Nm 3 / h, under the conditions of 1080°C and 0.1Mpa, the raw material mixture gas reacts to deposit polysilicon on the surface of the silicon core. When the silicon core grows to a diameter of 50mm, stop applying the current and adjust the flow rate of hydrogen to 200Nm 3 / h;
[0052] When the surface temperatur...
PUM
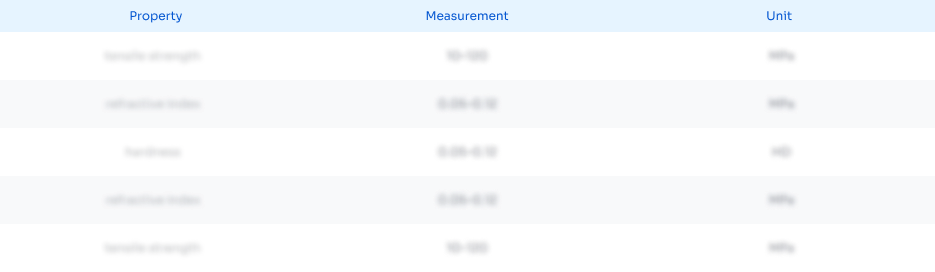
Abstract
Description
Claims
Application Information

- R&D
- Intellectual Property
- Life Sciences
- Materials
- Tech Scout
- Unparalleled Data Quality
- Higher Quality Content
- 60% Fewer Hallucinations
Browse by: Latest US Patents, China's latest patents, Technical Efficacy Thesaurus, Application Domain, Technology Topic, Popular Technical Reports.
© 2025 PatSnap. All rights reserved.Legal|Privacy policy|Modern Slavery Act Transparency Statement|Sitemap|About US| Contact US: help@patsnap.com