Method for realizing methanation of coke oven gas through carbon-replenishing hydrogen-returning process for synthetic natural gas
A technology of coke oven gas and methanation, which is applied in the petroleum industry, gas fuel, fuel, etc., can solve the problems of burning out catalyst, consumption of raw and auxiliary materials in production cost, and overheating of catalyst, so as to increase output and reduce unit energy consumption , the effect of high conversion rate
- Summary
- Abstract
- Description
- Claims
- Application Information
AI Technical Summary
Problems solved by technology
Method used
Image
Examples
Embodiment Construction
[0086] press now figure 1 , figure 2 Shown technological process and pipeline flow are set forth in detail as the best embodiment of the present invention and implement:
[0087] Process flow of the present invention comprises the steps:
[0088] 1. Compress the treated coke oven gas to 1.0MPa and enter the surge tank.
[0089] 2. The stabilized coke oven gas passes through the gas preheater 1, is heated to 250°C, and then enters the primary methanation reactor 2. A certain amount of self-produced water vapor is added to the primary methanation reactor 2. On the one hand, it can control Warm and heat removal, which is beneficial to the conversion of CO and can prevent CH 4 High temperature carbonation reaction.
[0090] 3. The temperature of the methanation gas in the primary methanation reactor 2 is about 600°C. After heat exchange in the waste heat boiler 5, the temperature is 250°C, and then enters the methanation reactor 3 in the carbon replenishment and hydrogen retu...
PUM
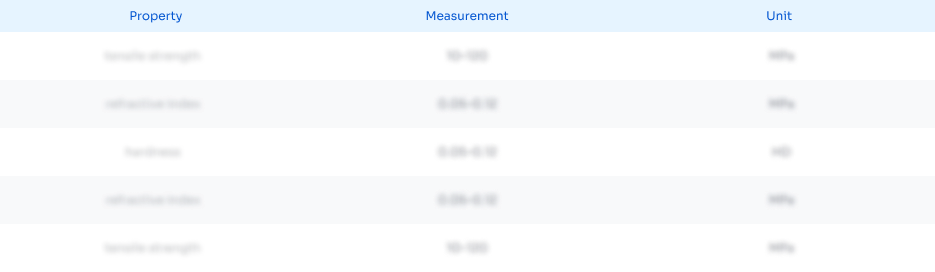
Abstract
Description
Claims
Application Information

- Generate Ideas
- Intellectual Property
- Life Sciences
- Materials
- Tech Scout
- Unparalleled Data Quality
- Higher Quality Content
- 60% Fewer Hallucinations
Browse by: Latest US Patents, China's latest patents, Technical Efficacy Thesaurus, Application Domain, Technology Topic, Popular Technical Reports.
© 2025 PatSnap. All rights reserved.Legal|Privacy policy|Modern Slavery Act Transparency Statement|Sitemap|About US| Contact US: help@patsnap.com