Process for manufacturing and molding double-layer plastic vehicle body
A molding process and plastic technology, applied in the coating and other directions, can solve the problems of uneven wall thickness of the plastic inner and outer sheets, increase the cost of raw materials, and complex production processes, and achieve no residual stress, simple structure, and simplified process. Effect
- Summary
- Abstract
- Description
- Claims
- Application Information
AI Technical Summary
Problems solved by technology
Method used
Image
Examples
Embodiment Construction
[0027] see figure 1 and figure 2 , taking automobile as an example, according to the manufacturing molding process of the double-layer plastic vehicle body provided by the present invention, comprises the steps:
[0028] (1) Make mould: make a die 1 and punch 2 respectively according to the outline of the automobile body, and set outer edge 11,21 respectively at the bottom of die 1 and punch 2;
[0029] (2) Roll out the hollow plastic body shell in the mold:
[0030] A. Feeding: Add powdery plastic raw materials between the die 1 and the punch 2, and then connect the outer edges 11 and 21 of the bottom of the die and the punch together to form an integral rotomolding mold 3;
[0031] B. Heating: Put the rotomolding mold into the heating chamber and make it rotate and heat continuously along the main axis and the auxiliary axis perpendicular to each other. The plastic raw materials in the mold are gradually evenly distributed and melted and adhered under the action of gravit...
PUM
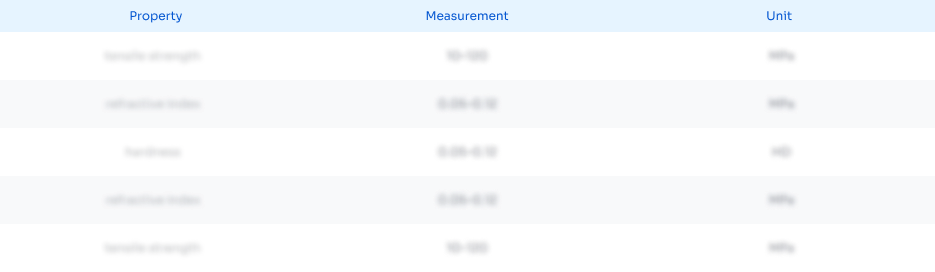
Abstract
Description
Claims
Application Information

- R&D
- Intellectual Property
- Life Sciences
- Materials
- Tech Scout
- Unparalleled Data Quality
- Higher Quality Content
- 60% Fewer Hallucinations
Browse by: Latest US Patents, China's latest patents, Technical Efficacy Thesaurus, Application Domain, Technology Topic, Popular Technical Reports.
© 2025 PatSnap. All rights reserved.Legal|Privacy policy|Modern Slavery Act Transparency Statement|Sitemap|About US| Contact US: help@patsnap.com