Method for manufacturing anodic foil of aluminum electrolytic capacitor
A technology for aluminum electrolytic capacitors and manufacturing methods, which is applied in the direction of electrolytic capacitors, capacitors, circuits, etc., can solve problems such as long hydration-resistant boosting time, decreased oxide film withstand voltage value, and fast boosting time recovery, etc., to improve product quality , the bending strength is improved, and the production process is simple
- Summary
- Abstract
- Description
- Claims
- Application Information
AI Technical Summary
Problems solved by technology
Method used
Image
Examples
Embodiment 1
[0013] Use a medium-pressure corroded foil with a purity of more than 99.99% to boil in pure water at 96°C for 5 minutes, then conduct a primary constant pressure 130V formation for 10 minutes in the formation solution of citric acid and its salts; Secondary constant voltage 280V formation for 10min in the formation solution of salts; followed by a third level constant pressure 315V formation for 20min in the formation solution of azelaic acid and its salts; heat treatment at 400°C for 1min; Press 315V for 10 minutes; perform phosphoric acid treatment in 1v / v% phosphoric acid solution at 80°C for 5 minutes; phosphating treatment is immersion treatment at 5v / v% concentration of phosphoric acid-based treatment agent at 80°C for 1min , the phosphoric acid-based treatment agent is phosphoric acid. The temperature of the second heat treatment is 400° C. for 1 min.
[0014] After testing for 3 months of storage, the variation of the voltage rise time of the oxide film of the anode ...
Embodiment 2
[0019] Use a high-pressure corroded foil with a purity of more than 99.99% to boil in pure water at 96°C for 10 minutes, then conduct a primary constant pressure 200V formation for 15 minutes in the formation solution of citric acid and its salts; Carry out secondary constant pressure 400V for 15min in a similar chemical forming solution; followed by a third level of constant pressure 530V for 30min in a chemical forming solution containing azelaic acid and its salts; heat treatment at 500°C for 3min; Press 530V for 15 minutes; carry out phosphoric acid treatment in 6v / v% phosphoric acid solution at 70°C for 10 minutes; phosphating treatment is immersion treatment at 60°C for 5 minutes at a concentration of phosphoric acid-based treatment agent of 2v / v% , the phosphoric acid-based treatment agent is phosphorous acid. Ammonium dihydrogen solution and 85% phosphorous acid. The temperature of the second heat treatment is 300° C. for 3 minutes.
[0020] After testing for 3 month...
Embodiment 3
[0025] Use a high-pressure corroded foil with a purity of more than 99.99% to boil in pure water at 96°C for 15 minutes, and then conduct a primary constant pressure 250V formation for 20 minutes in the formation solution of citric acid and its salts; Carry out secondary constant pressure 480V for 20min in the chemical forming liquid of azelaic acid and its salts; then carry out three-stage constant pressure 590V for 40min in the chemical forming liquid of azelaic acid and its salts; conduct heat treatment at 550°C for 5min; 590V for 20 minutes; phosphoric acid treatment in 10v / v% phosphoric acid solution at 60°C for 15 minutes; phosphating treatment is 10 minutes of immersion treatment at a concentration of phosphoric acid-based treatment agent at 1v / v% and a temperature of 20°C. The phosphoric acid-based treatment agent is 50 wt% ammonium dihydrogen phosphate solution and 50 wt% ammonium hypophosphite solution. The temperature of the second heat treatment is 80° C. for 5 min...
PUM
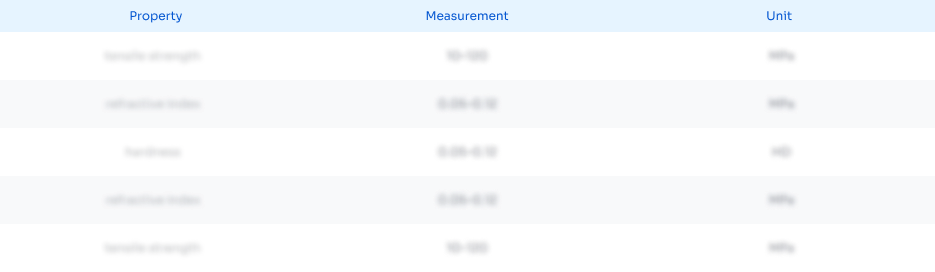
Abstract
Description
Claims
Application Information

- R&D
- Intellectual Property
- Life Sciences
- Materials
- Tech Scout
- Unparalleled Data Quality
- Higher Quality Content
- 60% Fewer Hallucinations
Browse by: Latest US Patents, China's latest patents, Technical Efficacy Thesaurus, Application Domain, Technology Topic, Popular Technical Reports.
© 2025 PatSnap. All rights reserved.Legal|Privacy policy|Modern Slavery Act Transparency Statement|Sitemap|About US| Contact US: help@patsnap.com