Finishing mill collar assembly and detection method
A technology for assembly testing and finishing mills, applied in metal rolling, length measuring devices, metal rolling, etc., can solve the problems of increasing spare parts cost, increasing downtime, wasting energy, etc., to improve assembly quality, improve physical quality, The effect of reducing the failure rate
- Summary
- Abstract
- Description
- Claims
- Application Information
AI Technical Summary
Problems solved by technology
Method used
Examples
Embodiment Construction
[0010] When checking the shaft head, remove the rust with water sandpaper, scrub the shaft head clean, check whether there are protrusions or sharp edges in the shaft head window, and if there are protrusions or sharp edges, use a steel file to grind them.
[0011] Use a standard taper sleeve and put it on the shaft head. Check whether the taper sleeve is in contact with the straight section of the shaft head. If the taper sleeve is not installed properly, it means that the straight section of the shaft head is deformed and contacts the taper sleeve. Grinding the shaft head. If it is not ground, it will be difficult to disassemble after assembly, and the taper sleeve may be pulled out, and the roller ring may even be scrapped. Generally, an outer diameter micrometer is used to measure the outer diameter of the taper sleeve after deformation at 5-6 points of the taper sleeve. , when the difference in average size is greater than or equal to 0.04mm, the size of the cone surface o...
PUM
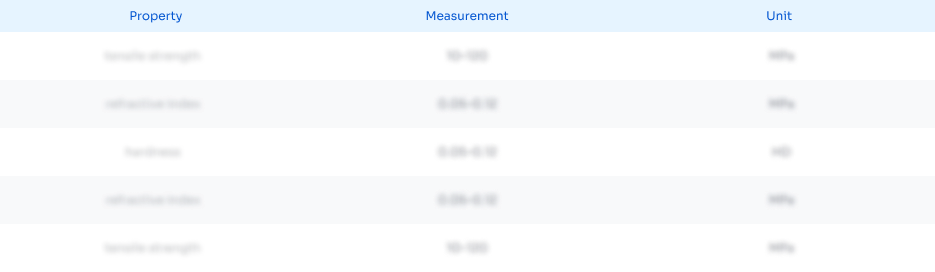
Abstract
Description
Claims
Application Information

- R&D
- Intellectual Property
- Life Sciences
- Materials
- Tech Scout
- Unparalleled Data Quality
- Higher Quality Content
- 60% Fewer Hallucinations
Browse by: Latest US Patents, China's latest patents, Technical Efficacy Thesaurus, Application Domain, Technology Topic, Popular Technical Reports.
© 2025 PatSnap. All rights reserved.Legal|Privacy policy|Modern Slavery Act Transparency Statement|Sitemap|About US| Contact US: help@patsnap.com