Travelling wave ultrasound motor with dual stator and rotor multi-diameter shaft structure
An ultrasonic motor, stepped shaft technology, applied in the direction of generator/motor, piezoelectric effect/electrostrictive or magnetostrictive motor, electrical components, etc. Problems such as small rotor mass, to achieve the effect of eliminating the pre-pressure adjustment mechanism, eliminating nonlinear superposition factors, and high mechanical efficiency
- Summary
- Abstract
- Description
- Claims
- Application Information
AI Technical Summary
Problems solved by technology
Method used
Image
Examples
Embodiment Construction
[0051] The disc-shaped traveling-wave ultrasonic motor with double-stator-rotor stepped shaft structure of the present invention is based on the original single-stator-rotor disc-shaped traveling-wave ultrasonic motor (that is, the first type of motor), and the external dimensions of the end faces of the two motors can be kept consistent , the piezoelectric ceramic sheet in the stator, the stator vibrating body and the stator base can use the original parts. The rotor that matches the stepped shaft only needs to adjust the inner diameter, and the material and thickness of the friction contact layer on the rotor are unchanged. The original dome shape is simplified to a cylindrical shape and the thrust bearing therein is omitted. In this way, most parts of the two ultrasonic motors are interchangeable, and the corresponding machining is simplified.
[0052] The external fixing structure of the present invention is realized by fixing the upper and lower stator bases on the two en...
PUM
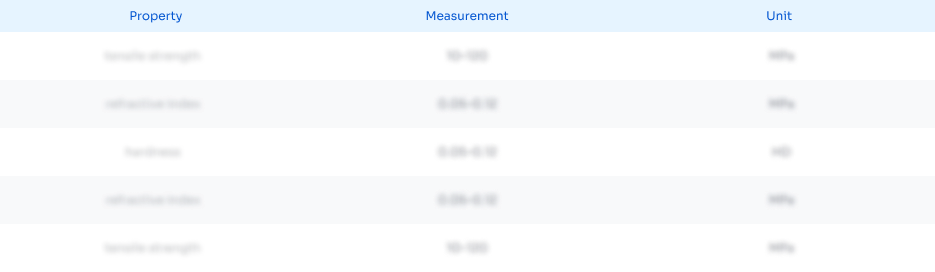
Abstract
Description
Claims
Application Information

- Generate Ideas
- Intellectual Property
- Life Sciences
- Materials
- Tech Scout
- Unparalleled Data Quality
- Higher Quality Content
- 60% Fewer Hallucinations
Browse by: Latest US Patents, China's latest patents, Technical Efficacy Thesaurus, Application Domain, Technology Topic, Popular Technical Reports.
© 2025 PatSnap. All rights reserved.Legal|Privacy policy|Modern Slavery Act Transparency Statement|Sitemap|About US| Contact US: help@patsnap.com