Method for preparing metal magnesium by silicothermic process
A reduction method and metal magnesium technology are applied in the field of inorganic salt chemical industry, which can solve the problems of endangering the safety of operators, environmental pollution, and high requirements for anti-corrosion of equipment, and achieve the effects of high utilization rate and high total yield.
- Summary
- Abstract
- Description
- Claims
- Application Information
AI Technical Summary
Problems solved by technology
Method used
Examples
Embodiment 1
[0028] Embodiment 1, get 70ml saturated magnesium chloride solution (concentration is 4.7497mol / L), add 490ml water (dilute to 8 times volume, magnesium chloride concentration is 0.5937mol / L), add 40g lime (magnesium chloride / lime mol ratio is 1: 2.08 ), stirred for 4 hours. Settled for 20 minutes, vacuum filtered, washed once with 70ml of water, and dried. The calcium-magnesium ratio in the calcium-magnesium mixed hydroxide generated is 1:1.05, Cl - The content is 1.0%, and the magnesium yield is 100%. The calcium-magnesium mixed hydroxide was placed in a horse boiling furnace and calcined at 800° C. for 4 hours to obtain the calcium-magnesium mixed oxide with a water activity of 36.02%. Mix this calcium magnesium mixed oxide with 75% ferrosilicon, fluorite (CaF 2 ) were mixed at a mass ratio of 80.46%, 16.45%, and 3.09%, respectively, and dry-milled with a ball mill until the particle size was 90% and passed through a 200-mesh sieve, and then pressed into tablets under a ...
Embodiment 2
[0029] Embodiment 2, get 70ml saturated magnesium chloride solution (concentration is 4.7497mol / L). Get 40g of lime, add 450ml of water, stir to prepare lime slurry. The obtained lime slurry was mixed and reacted with saturated magnesium chloride solution (magnesium chloride / lime molar ratio was 1:2.08), stirred for 0.5 hour to obtain jelly, which was vacuum filtered. After filtering, wash with 70ml of water each time, wash 3 times in total, and dry. The calcium-magnesium ratio in the generated calcium-magnesium mixed hydroxide is 1:1.39, Cl - The content is 10.08%, and the magnesium yield is 100%. The calcium-magnesium mixed hydroxide was placed in a horse boiling furnace and calcined at 800° C. for 4 hours to obtain a calcium-magnesium mixed oxide with a water activity of 34.91%. Mix this mixed oxide with 75% ferrosilicon, fluorite (CaF 2) were mixed at a mass ratio of 80.46%, 16.45%, and 3.09%, and dry-milled with a ball mill until the particle size was 90% and passed t...
Embodiment 3
[0030] Embodiment 3, get 70ml saturated magnesium chloride solution (concentration is 4.7497mol / L), add 350ml water (dilute to 6 times volume), add 40g lime (magnesium chloride / lime molar ratio is 1: 2.08), stir 4 hours. Settled for 20 minutes, centrifugally filtered, washed once with 70ml of water, and dried. The calcium-magnesium ratio in the calcium-magnesium mixed hydroxide generated is 1:1.06, Cl - The content is 1.6%, and the magnesium yield is 100%. The calcium-magnesium mixed hydroxide was placed in a horse boiling furnace and calcined at 800° C. for 4 hours to obtain a calcium-magnesium mixed oxide with a water activity of 36.02%. Mix this mixed oxide with 75% ferrosilicon, fluorite (CaF 2 ) are mixed at a mass ratio of 80.46%, 16.45%, and 3.09%, dry-milled with a ball mill until the particle size is 90%, and passed through a 200-mesh sieve, and then pressed into tablets with a tablet machine under a pressure of 200MPa, and then placed in a vacuum tank. Reduction w...
PUM
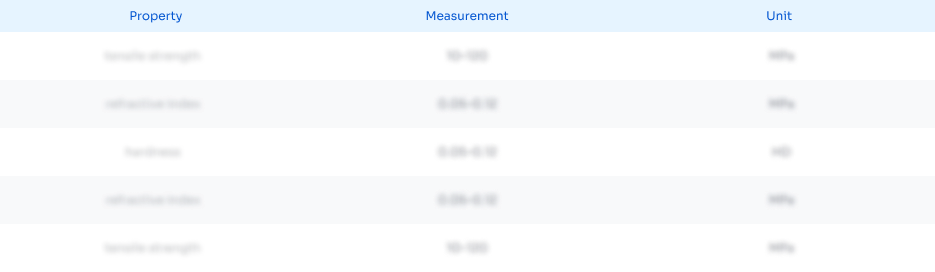
Abstract
Description
Claims
Application Information

- R&D
- Intellectual Property
- Life Sciences
- Materials
- Tech Scout
- Unparalleled Data Quality
- Higher Quality Content
- 60% Fewer Hallucinations
Browse by: Latest US Patents, China's latest patents, Technical Efficacy Thesaurus, Application Domain, Technology Topic, Popular Technical Reports.
© 2025 PatSnap. All rights reserved.Legal|Privacy policy|Modern Slavery Act Transparency Statement|Sitemap|About US| Contact US: help@patsnap.com