Precision-forging chemical-milling solution for high-temperature alloy blades and chemical milling method
A superalloy and solution technology, which is applied in the field of superalloy blade precision forging, chemical milling, and chemical milling, can solve problems such as inability to find, and achieve the effects of easy cleaning, less environmental pollution, and less impact
- Summary
- Abstract
- Description
- Claims
- Application Information
AI Technical Summary
Problems solved by technology
Method used
Image
Examples
Embodiment 1
[0042] This embodiment is a group of GH4169 precision forged blades, 20 in total, and it is required to remove 0.5mm of material by chemical milling.
[0043] The high-temperature alloy blade precision forging and milling solution used in this embodiment includes 55 g / L hydrochloric acid, 135 g / L nitric acid and 450 g / L ferric chloride, and the rest is water. One liter of solution is prepared as follows: first add a small amount of water to the container, take 50mL of hydrochloric acid with a specific gravity of 1.14 and 90mL of nitric acid with a specific gravity of 1.5, pour them into water, and stir evenly; weigh 450g of ferric chloride and add it, and finally add water to one liter .
[0044] In this embodiment, the specific steps of chemical milling of precision forging blades are as follows:
[0045] Step 1, size grouping: measure the blade body size of the part with an inductance meter, and the removal amount on one side is 0.5mm.
[0046] Step 2, degreasing: use wate...
Embodiment 2
[0063] This embodiment is a group of GH4169 precision forged blades, a total of 15 blades, which require 0.4mm of material removal by chemical milling.
[0064]The high-temperature alloy blade precision forging milling solution used in this embodiment includes 75g / L hydrochloric acid, 125g / L nitric acid and 400g / L ferric chloride, and the rest is water. One liter of solution is prepared as follows: first add a small amount of water to the container, take 65mL of hydrochloric acid with a specific gravity of 1.14 and 85mL of nitric acid with a specific gravity of 1.5, pour them into water, and stir evenly; weigh 400g of ferric chloride and add it, and finally add water to one liter .
[0065] In this embodiment, the specific steps of chemical milling of precision forging blades are as follows:
[0066] Step 1, size grouping: measure the leaf body size of the part with an inductance meter, and the removal amount on one side is 0.4mm.
[0067] Step 2, degreasing: use water-based...
Embodiment 3
[0084] This embodiment is a group of GH4169 precision forged blades, a total of 15 blades, which require 0.3mm of material removal by chemical milling. The high-temperature alloy blade precision forging and milling solution used in this embodiment includes 65g / L hydrochloric acid, 100g / L nitric acid and 500g / L ferric chloride, and the rest is water. One liter of solution is prepared as follows: first add a small amount of water to the container, take 57mL of hydrochloric acid with a specific gravity of 1.14 and 70mL of nitric acid with a specific gravity of 1.5, pour them into water, and stir evenly; weigh 500g of ferric chloride and add it, and finally add water to one liter .
[0085] In this embodiment, the specific steps of chemical milling of precision forging blades are as follows:
[0086] Step 1, size grouping: measure the blade body size of the part with an inductance meter, and the removal amount on one side is 0.3mm.
[0087] Step 2, degreasing: use water-based cl...
PUM
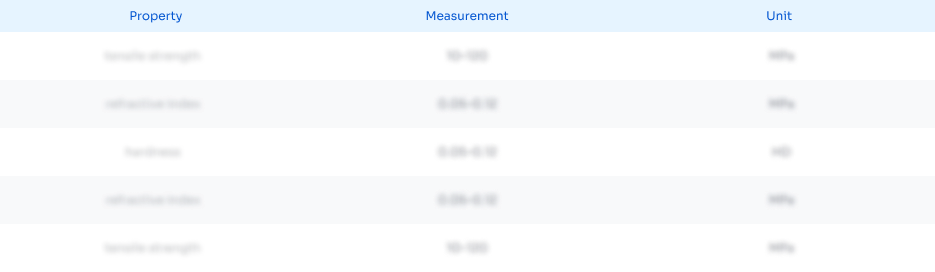
Abstract
Description
Claims
Application Information

- R&D
- Intellectual Property
- Life Sciences
- Materials
- Tech Scout
- Unparalleled Data Quality
- Higher Quality Content
- 60% Fewer Hallucinations
Browse by: Latest US Patents, China's latest patents, Technical Efficacy Thesaurus, Application Domain, Technology Topic, Popular Technical Reports.
© 2025 PatSnap. All rights reserved.Legal|Privacy policy|Modern Slavery Act Transparency Statement|Sitemap|About US| Contact US: help@patsnap.com