Optical element manufacturing method and optical element
一种光学元件、制造方法的技术,应用在光学元件、光学头制造、光学等方向
- Summary
- Abstract
- Description
- Claims
- Application Information
AI Technical Summary
Problems solved by technology
Method used
Image
Examples
Embodiment 1~5
[0101] use Figure 6 The molding die 30 shown produces a figure 1 The optical element 10 is shown. The materials of the upper mold 31, the lower mold 32 and the side mold 33 all adopt superhard materials with tungsten carbide as the main component. The heating temperature of the molding die 30 was 450° C. for the upper die 31 , 470° C. for the lower die 32 , and 470° C. for the side die 33 .
[0102] The optical surface 11c of the optical element 10 is a cylindrical surface, and the section perpendicular to the generatrix is formed by an arc with a radius of 3mm. The optical surface 12c is a cylindrical surface, and the section perpendicular to the generatrix is formed by an arc with a radius of 2mm. The thickness of the central part was made 4 mm. Additionally, make image 3 The shown extended upper forming surface 110 has a circumference of 4 mm x 4 mm, and the extended side forming surface 132 has a height of 4.1 mm. At this moment, the volume of the most filled sp...
PUM
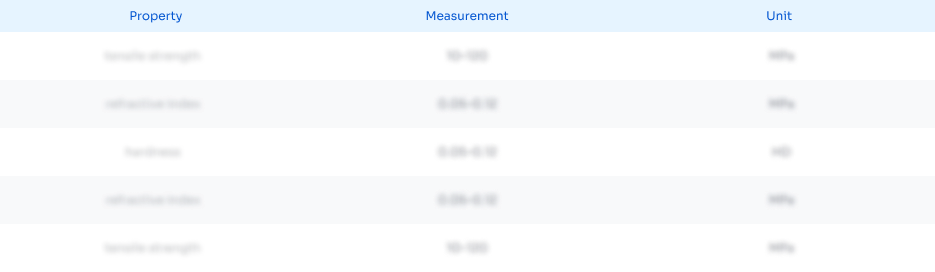
Abstract
Description
Claims
Application Information

- R&D Engineer
- R&D Manager
- IP Professional
- Industry Leading Data Capabilities
- Powerful AI technology
- Patent DNA Extraction
Browse by: Latest US Patents, China's latest patents, Technical Efficacy Thesaurus, Application Domain, Technology Topic, Popular Technical Reports.
© 2024 PatSnap. All rights reserved.Legal|Privacy policy|Modern Slavery Act Transparency Statement|Sitemap|About US| Contact US: help@patsnap.com