Six-dimensional force sensor
A six-dimensional force sensor and sensor technology, applied in the direction of instruments, measuring force, measuring devices, etc., can solve the problems of reducing the Z-direction stiffness of the disk structure, reducing the dynamic performance of the sensor, and increasing the axial size, etc., to achieve an enhanced force solution. Coupling effect, compact structure, the effect of increasing the Z-direction range and stiffness
- Summary
- Abstract
- Description
- Claims
- Application Information
AI Technical Summary
Problems solved by technology
Method used
Image
Examples
Embodiment Construction
[0023] This embodiment is a six-dimensional force sensor for the foot of a quadruped bionic robot.
[0024] In this embodiment, the measuring range is determined according to the motion requirements of the robot. The force range of Fz is 2000N, the force range of Fx and Fy is 1500N, and the torque range of Mz, Mx and My is 75Nm. According to the measuring range, the key dimensions of the elastic body of the sensor are determined as follows: The thickness of the elastic beam and the lower elastic beam is 2mm, the maximum outer diameter of the sensor elastic body is φ45mm, and the overall height is 32mm.
[0025] Such as figure 1 As shown, this embodiment includes a sensor elastic body and a resistance strain gauge, and the elastic body is composed of a cylindrical shell and a cross elastic beam structure. The shell is hollowed out to form the flexible beam 2, the upper elastic beam 4, the force transmission column 7, the lower elastic beam 8, the upper boss 5, the lower boss 9...
PUM
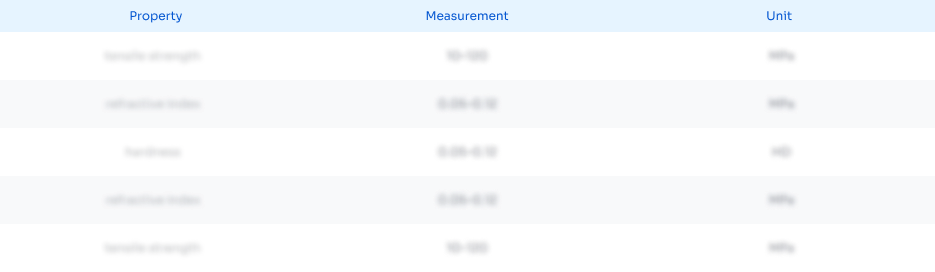
Abstract
Description
Claims
Application Information

- R&D
- Intellectual Property
- Life Sciences
- Materials
- Tech Scout
- Unparalleled Data Quality
- Higher Quality Content
- 60% Fewer Hallucinations
Browse by: Latest US Patents, China's latest patents, Technical Efficacy Thesaurus, Application Domain, Technology Topic, Popular Technical Reports.
© 2025 PatSnap. All rights reserved.Legal|Privacy policy|Modern Slavery Act Transparency Statement|Sitemap|About US| Contact US: help@patsnap.com