Bearing retainer and machining technique thereof
A bearing retainer and processing technology, used in bearing components, shafts and bearings, mechanical equipment, etc., can solve the problems of load capacity and working temperature limitations, low operating temperature, and high overall cost, and improve product accuracy and reliability. performance, avoid waste, and improve utilization
- Summary
- Abstract
- Description
- Claims
- Application Information
AI Technical Summary
Problems solved by technology
Method used
Image
Examples
Embodiment Construction
[0031] figure 1 In the illustrated embodiment, a processing technique for a bearing retainer is characterized in that it mainly includes the following steps
[0032] 1. Blanking: According to the required bearing capacity of the bearing to be processed, calculate the circumferential length and height of the retainer that needs to be processed to install the locking cylindrical roller, and punch the used low-carbon steel material according to the calculated size. Long strips that meet the circumferential length and height of the stamping holder;
[0033] 2. Punch out all the pockets at one time: install and use the cylindrical roller size of the bearing according to the needs, and use the stamping die to punch out all the pockets that need to lock the cylindrical roller at one time. , Including the locking surface structure of punched pocket structure and its oblique slope structure;
[0034] 3. Stamp the groove structure of all pocket beams at one time: use a stamping die to punch a...
PUM
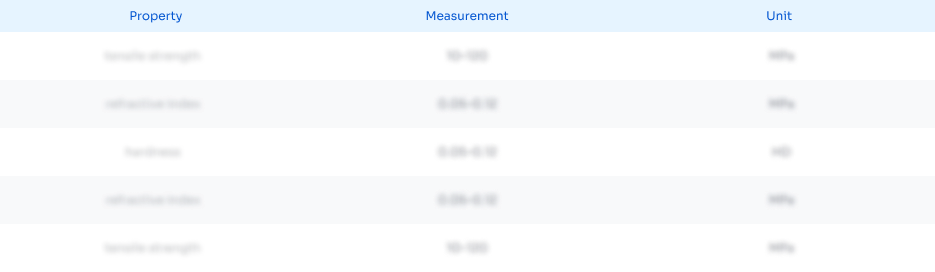
Abstract
Description
Claims
Application Information

- R&D
- Intellectual Property
- Life Sciences
- Materials
- Tech Scout
- Unparalleled Data Quality
- Higher Quality Content
- 60% Fewer Hallucinations
Browse by: Latest US Patents, China's latest patents, Technical Efficacy Thesaurus, Application Domain, Technology Topic, Popular Technical Reports.
© 2025 PatSnap. All rights reserved.Legal|Privacy policy|Modern Slavery Act Transparency Statement|Sitemap|About US| Contact US: help@patsnap.com