Carbon fiber reinforced wood composite material and preparation method thereof
A composite material and carbon fiber technology, which is applied in the direction of wood layered products, wood processing equipment, and wooden veneer joints, can solve the problems of poor performance of wood composite materials and high cost of carbon fiber, and achieve convenient operation, reduced variability, Avoid costly effects
- Summary
- Abstract
- Description
- Claims
- Application Information
AI Technical Summary
Problems solved by technology
Method used
Image
Examples
Embodiment Construction
[0015] Let’s illustrate with an example in conjunction with the accompanying drawings:
[0016] After the log is sawn into sawn timber, the target moisture content of drying is 12%, and the moisture content after drying can be 8-12%. Afterwards, the sawn timber is finished, and the finger joints are milled out. The length of the finger joints is 10, or 12, or 15, or 20, or 25, or 30, or 35mm. Apply latex glue to one side of the processed wood laminate 2 ends, the glue amount is: 100, or 200, or 300, or 400, or 500, or 600, or 700g / m 2 . Appropriate pressure is applied longitudinally to the finger joint 3, the end pressure is 4, or 5, or 6, or 7, or 8MPa, and the end pressure time is 1, or 2, or 3, or 4, or 5, or 6, Or 7, or 8s. After the end pressure is completed, keep in good health for more than 24 hours. Apply isocyanate glue to one side of the processed wood laminate 2, and the glue amount is: 100, or 200, or 300, or 400, or 500, or 600, or 700g / m 2 . Carry out blank...
PUM
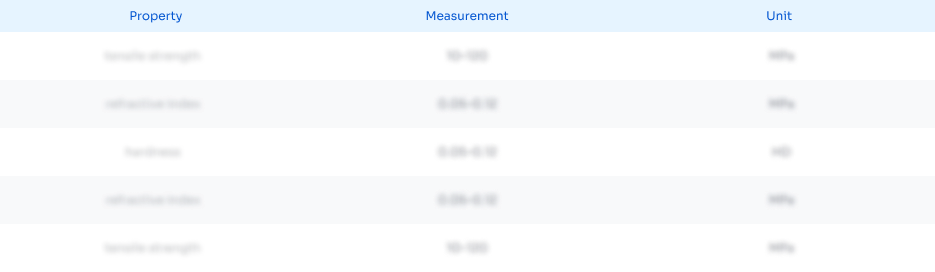
Abstract
Description
Claims
Application Information

- R&D
- Intellectual Property
- Life Sciences
- Materials
- Tech Scout
- Unparalleled Data Quality
- Higher Quality Content
- 60% Fewer Hallucinations
Browse by: Latest US Patents, China's latest patents, Technical Efficacy Thesaurus, Application Domain, Technology Topic, Popular Technical Reports.
© 2025 PatSnap. All rights reserved.Legal|Privacy policy|Modern Slavery Act Transparency Statement|Sitemap|About US| Contact US: help@patsnap.com