Composite silicon-free defoamer
A defoamer and composite technology, which is applied in the field of petrochemical products and composite silicon-free defoamers, can solve the problems of shortening the running time of the device and catalyst deactivation
- Summary
- Abstract
- Description
- Claims
- Application Information
AI Technical Summary
Problems solved by technology
Method used
Image
Examples
Embodiment 1
[0017] Embodiment 1: Weigh raw materials according to the following ratio: 20Kg of lauryl alcohol, 35Kg of polyoxyethylene polyoxypropylene glyceryl ether, 15Kg of ethoxypropoxylate of phenol derivatives, 30Kg of isooctyl alcohol, the polyoxyethylene polyoxypropylene The relative molecular weight of oxypropylene glyceryl ether is greater than 15,000. Add the above-mentioned raw materials into a reaction vessel with a heating device, heat and stir at 70° C. for 3 hours, and stir evenly to form the composite silicon-free defoamer.
Embodiment 2
[0018] Example 2: Weigh raw materials according to the following proportions: 30Kg of lauryl alcohol, 30Kg of polyoxyethylene polyoxypropylene glyceryl ether, 15Kg of ethoxypropoxylate of phenol derivatives, and 25Kg of isooctyl alcohol. The relative molecular weight of the polyoxyethylene polyoxypropylene glyceryl ether is greater than 15,000. Add the above-mentioned raw materials into a reaction vessel with a heating device, heat and stir at 70° C. for 3 hours, and stir evenly to form the composite silicon-free defoamer.
Embodiment 3
[0019] Example 3: raw materials were weighed according to the following proportions: 35Kg of lauryl alcohol, 45Kg of polyoxyethylene polyoxypropylene glyceryl ether, 5Kg of phenol derivative ethoxypropoxylate, and 15Kg of isooctyl alcohol. The relative molecular weight of the polyoxyethylene polyoxypropylene glyceryl ether is greater than 15,000. Add the above-mentioned raw materials into a reaction vessel with a heating device, heat and stir at 70° C. for 3 hours, and stir evenly to form the composite silicon-free defoamer.
PUM
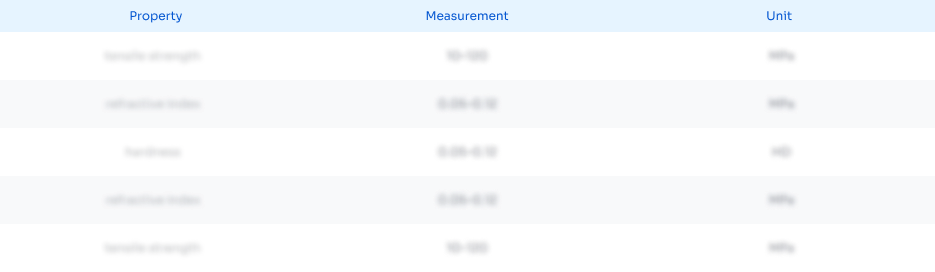
Abstract
Description
Claims
Application Information

- R&D Engineer
- R&D Manager
- IP Professional
- Industry Leading Data Capabilities
- Powerful AI technology
- Patent DNA Extraction
Browse by: Latest US Patents, China's latest patents, Technical Efficacy Thesaurus, Application Domain, Technology Topic, Popular Technical Reports.
© 2024 PatSnap. All rights reserved.Legal|Privacy policy|Modern Slavery Act Transparency Statement|Sitemap|About US| Contact US: help@patsnap.com