Cross wedge rolling forming method of hollow shaft head of automobile rear bridge
A technology for rear axles and hollow shafts of automobiles, applied in metal rolling and other directions, can solve the problems of easy lateral flow of metal, large equipment and investment, and inability to obtain parts, so as to reduce machining allowance, high material utilization rate, no shock effect
- Summary
- Abstract
- Description
- Claims
- Application Information
AI Technical Summary
Problems solved by technology
Method used
Image
Examples
Embodiment 1
[0025] The cross-wedge rolling two-circle rolling forming process is adopted, and two pairs of wedges are processed on a pair of roller molds to complete the rolling of the hollow shaft head. Heat the seamless steel pipe to 950°C, penetrate the mandrel, the difference between the diameter of the mandrel and the inner diameter of the steel pipe is not more than 1mm, and send it into the first pass between the two molds through the axial pushing device. The steel pipe with the mandrel makes a rotary motion under the action of the first pair of wedges, and the middle part of the rolled piece is rolled into shape, such as image 3 shown. Then push the rolled piece into the second pair of holes in the axial direction, and the second pair of wedges will participate in the rolling and forming when the die rotates for the second time, such as Figure 4 shown. The formed hollow shaft head blank is pushed out from between the two molds by the axial pushing device, and the mandrel is e...
Embodiment 2
[0028] The cross-wedge rolling two-circle rolling forming process is adopted, and two pairs of wedges are processed on a pair of roller molds to complete the rolling of the hollow shaft head. Heat the seamless steel pipe to 1100°C, penetrate the mandrel, the difference between the diameter of the mandrel and the inner diameter of the steel pipe is not more than 1mm, and send it into the first pass between the two molds through the axial pushing device. The steel pipe with the mandrel makes a rotary motion under the action of the first pair of wedges, and the middle part of the rolled piece is rolled into shape, such as image 3 shown. Then push the rolled piece into the second pair of holes in the axial direction, and the second pair of wedges will participate in the rolling and forming when the die rotates for the second time, such as Figure 4 shown. The formed hollow shaft head blank is pushed out from between the two molds by the axial pushing device, and the mandrel is ...
Embodiment 3
[0031] The cross-wedge rolling two-circle rolling forming process is adopted, and two pairs of wedges are processed on a pair of roller molds to complete the rolling of the hollow shaft head. Heat the seamless steel pipe to 800°C, penetrate the mandrel, the difference between the diameter of the mandrel and the inner diameter of the steel pipe is not more than 1mm, and send it into the first pass between the two molds through the axial pusher device. The steel pipe with the mandrel makes a rotary motion under the action of the first pair of wedges, and the middle part of the rolled piece is rolled into shape, such as image 3 shown. Then push the rolled piece into the second pair of holes in the axial direction, and the second pair of wedges will participate in the rolling and forming when the die rotates for the second time, such as Figure 4 shown. The formed hollow shaft head blank is pushed out from between the two molds by the axial pushing device, and the mandrel is ej...
PUM
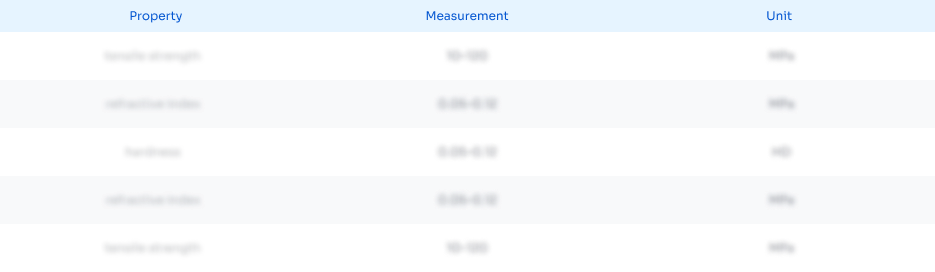
Abstract
Description
Claims
Application Information

- Generate Ideas
- Intellectual Property
- Life Sciences
- Materials
- Tech Scout
- Unparalleled Data Quality
- Higher Quality Content
- 60% Fewer Hallucinations
Browse by: Latest US Patents, China's latest patents, Technical Efficacy Thesaurus, Application Domain, Technology Topic, Popular Technical Reports.
© 2025 PatSnap. All rights reserved.Legal|Privacy policy|Modern Slavery Act Transparency Statement|Sitemap|About US| Contact US: help@patsnap.com