Device for dry etching
A technology of dry etching and etching gas, applied in the manufacture of electrical components, circuits, semiconductor/solid-state devices, etc., can solve problems such as low production efficiency, and achieve the effect of improving production efficiency and production speed
- Summary
- Abstract
- Description
- Claims
- Application Information
AI Technical Summary
Problems solved by technology
Method used
Image
Examples
Embodiment 1
[0033] image 3 It is a schematic diagram of Embodiment 1 of the present invention. Such as image 3 As shown, the dry etching device includes: a chamber 1 for etching; a chamber door 101 arranged on the side of the chamber 1 for transferring the substrate; a base 102 erected at the bottom of the chamber 1 for placing the substrate 4; An inlet 2 for blowing etching gas into the chamber 1; an inlet pipe 201 communicating the inlet 2 with the top of the chamber 1, so that the etching gas is blown in from the top of the chamber 1; The aspirator 3 for extracting the etching gas in the chamber 1; the aspirator 301 communicating the aspirator 3 with the bottom of the chamber 1; The etching gas in the chamber 1 is an auxiliary pumping device for controlling the contact density of the etching gas and the substrate 4, and the auxiliary pumping device is composed of an auxiliary pumping device 5 and an auxiliary pumping pipe 501 capable of controlling the pumping volume. Specifically...
Embodiment 2
[0040] Figure 4 It is a schematic diagram of Embodiment 2 of the present invention. Such as Figure 4 As shown, the dry etching device includes: a chamber 1 for etching; a chamber door 101 arranged on the side of the chamber 1 for transferring the substrate; a base 102 erected at the bottom of the chamber 1 for placing the substrate 4; An inlet 2 for blowing etching gas into the chamber 1; an inlet pipe 201 communicating the inlet 2 with the top of the chamber 1, so that the etching gas is blown in from the top of the chamber 1; The aspirator 3 for extracting the etching gas in the chamber 1; the aspirator 301 communicating the aspirator 3 with the bottom of the chamber 1; The etching gas in the chamber 1 is used to control the contact density of the etching gas and the substrate 4. The auxiliary pumping equipment is composed of an auxiliary pumping pipe 501 and a valve 6 for controlling the pumping volume of the auxiliary pumping pipe. The auxiliary pumping pipe 501 One end...
Embodiment 3
[0046] Figure 5 It is a schematic diagram of Embodiment 3 of the present invention. Such as Figure 5 As shown, the dry etching device includes: a chamber 1; a chamber door 101 arranged on the side of the chamber 1 for transferring substrates; a base 102 erected at the bottom of the chamber 1 for placing the substrate 4; Intaker 2 for blowing etching gas into 1; Inlet pipe 201 connecting the inlet 2 and the top of chamber 1, so that etching gas is blown in from the top of chamber 1; used to extract etching from chamber 1 The air extractor 3 of the gas; the exhaust pipe connecting the air extractor 3 and the bottom of the chamber 1; the upper casing 7 and the lower casing 8 which can be tightly nested with each other are also arranged in the chamber 1, and the lower casing The bottom of 8 is provided with a suction port, and the side of the lower shell 8 is provided with an auxiliary suction port 9, the horizontal position of the auxiliary suction port 9 is higher than the h...
PUM
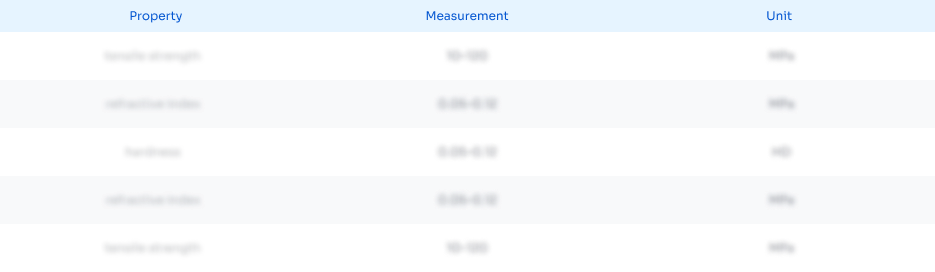
Abstract
Description
Claims
Application Information

- R&D
- Intellectual Property
- Life Sciences
- Materials
- Tech Scout
- Unparalleled Data Quality
- Higher Quality Content
- 60% Fewer Hallucinations
Browse by: Latest US Patents, China's latest patents, Technical Efficacy Thesaurus, Application Domain, Technology Topic, Popular Technical Reports.
© 2025 PatSnap. All rights reserved.Legal|Privacy policy|Modern Slavery Act Transparency Statement|Sitemap|About US| Contact US: help@patsnap.com